
As the desire for hydrogen as a clean energy source intensifies, the current midstream strategy is to transport hydrogen and hydrogen fuel blends through legacy piping networks. There is limited data on the impact of hydrogen transport on the properties (fatigue, fracture toughness, crack growth rates, etc.) and life cycles of these pipe systems. In addition, there is a wide range of steel grades, weld methods, and material quality associated with legacy oil and gas pipelines. All of these factors will influence the benefits of hydrogen and will require significant testing and analysis to fully understand.
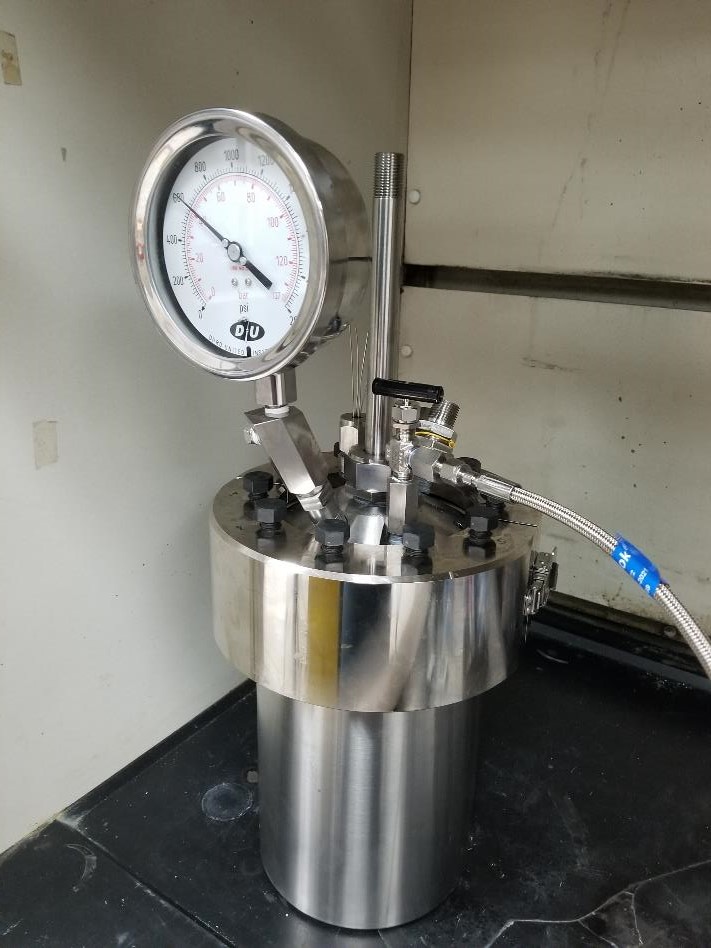
Within the next few months, a new technique developed by EWI for testing fracture mechanics in a controlled environment will be implemented using a pressure vessel with a sliding seal on the pull rod allowing for mechanical property measurements under pressure. Initially, fracture toughness studies will be conducted with compact tension (C(T)) specimens. Wires, which will be used for direct current potential drop (DC/PD) measurements on the C(T) specimen, will also be sealed in the vessel. DC/PD measures the change in resistance of a specimen which can be correlated directly with crack growth due to hydrogen exposure. The pressure vessel will be integrated into a servo-electric load frame with initial target test pressures up to 3000 psi.
States like California and New York are already pushing operators to transport hydrogen mixes with natural gas. The information from this test capability will help operators better handle the challenge of safely flowing hydrogen and hydrogen fuel blends through their pipeline network.
Questions about EWI’s fracture mechanics testing? Contact Jesse Rhodes, Applications Engineer at [email protected] or 614.688.5147.