
With advancements in additive manufacturing, interest has grown in functionally graded materials (FGMs) as the gradual variations in their composition can provide locally tailored properties. However, they are plagued by a familiar challenge in the world of multi-material solutions – effective joining.
The broad range of composition in FGMs can lead to several problems, most notably a mismatch between coefficients of thermal expansion and detrimental or brittle phases that compromise strength, cause cracks upon heating and prohibit welding. To combat these problems, software platforms such as CALPHAD offer tools to generate isothermal phase diagrams that help plan gradient paths to avoid detrimental phases. But these tools require users to visualize and navigate high-dimensional spaces.
Olga Eliseeva, Materials Project Engineer at EWI, has developed a machine-learning methodology to move from one metal to another without problematic phases. With this technique, undesirable regions – or “obstacles” – are mapped out, while an algorithm identifies a path in the composition space that can avoid those obstacles.
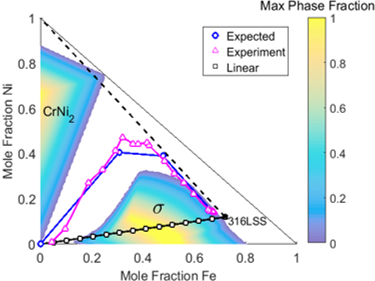
Eliseeva created and tested the path-planning approach for deleterious phase avoidance in additively manufactured FGMs for her doctoral thesis. She designed a functional gradient, planning a path from 316L stainless steel to pure chromium, then 3D-printed bulk samples with a multi-material direct laser deposition system. The samples were heat treated for eight hours at 900ºC and characterized in both as-deposited and heat-treated states to ascertain local compositions, microstructure and phase constituents. The functional gradient completely eliminated the detrimental phase after heat treatment.
In a second experiment, Eliseeva planned a path from an iron/chromium alloy to tungsten, which presented challenges as there is a nearly 2000ºC difference in the melting temperatures between the materials. There was no oxidation, visible cracking, or detrimental phase midway through the 3D-printing process. While there was slight cracking near 100% chromium midpoint of the full gradient print, 100% tungsten was reached with no cracking.
While this path-planning technique has not yet moved from development to application, Eliseeva sees potential for the methodology not only in additive manufacturing, but also in resistance sintering and multi-layer welding applications for automotive, aerospace, nuclear and other markets.
“This technique can be applied across industries,” says Eliseeva. “We are looking at how materials, combined with machine learning, can help us move theory into reality and create mechanically strong pieces from steel and aluminum or other materials that a few years ago were unthinkable.”
Questions about path planning to avoid detrimental phases in functional gradients? Contact Olga Eliseeva at [email protected] or614.688.5268.