
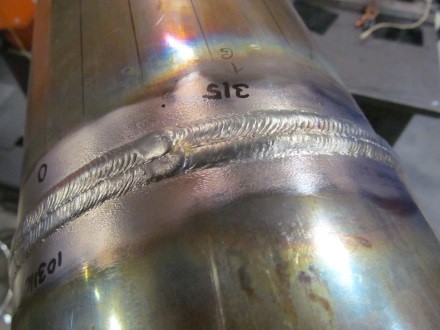
Virtually all ship designs utilize copper-nickel alloys for applications such as fire mains and other seawater/freshwater piping, tanks, and structures such as rope guards and fairings. The manual gas tungsten arc welding (GTAW) process that is typically used to weld copper-nickel pipe joints has relatively low productivity due to slow travel speeds and low deposition rates. The implementation of pulsed gas metal arc welding (GMAW-P) can yield significant productivity benefits for semi-automatic, mechanized, and robotic applications through faster travel speeds and increased deposition rates.
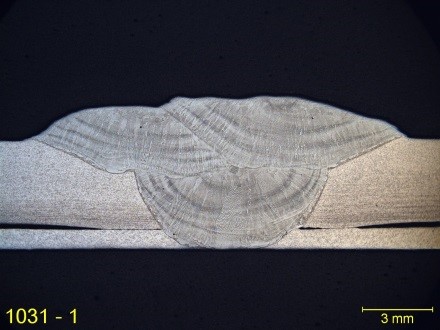
EWI has recently demonstrated the feasibility of semi-automatic and robotic GMAW-P for all-position welding of copper-nickel pipe joints for welding in both the pipe shop and onboard the ship. Engineering Group Leader Nick Kapustka and Business Development Director for Government Programs Paul Blomquist present this work in a new paper, GMAW-P Welding of Copper-nickel Pipe Joints for Shipbuilding Applications. The findings show that by combining advanced GMAW welding systems with optimized welding procedures, the barriers that have historically limited the use of the GMAW-P process for copper-nickel pipe joints were overcome, with significant gains in productivity.
To view/download GMAW-P Welding of Copper-nickel Pipe Joints for Shipbuilding Applications, click here.
To contact the authors of this paper, email [email protected] or [email protected].