
Reducing Waste, Cost, and Effort and Cost Within Manufacturing Companies: An Independent Perspective
by James Cruz
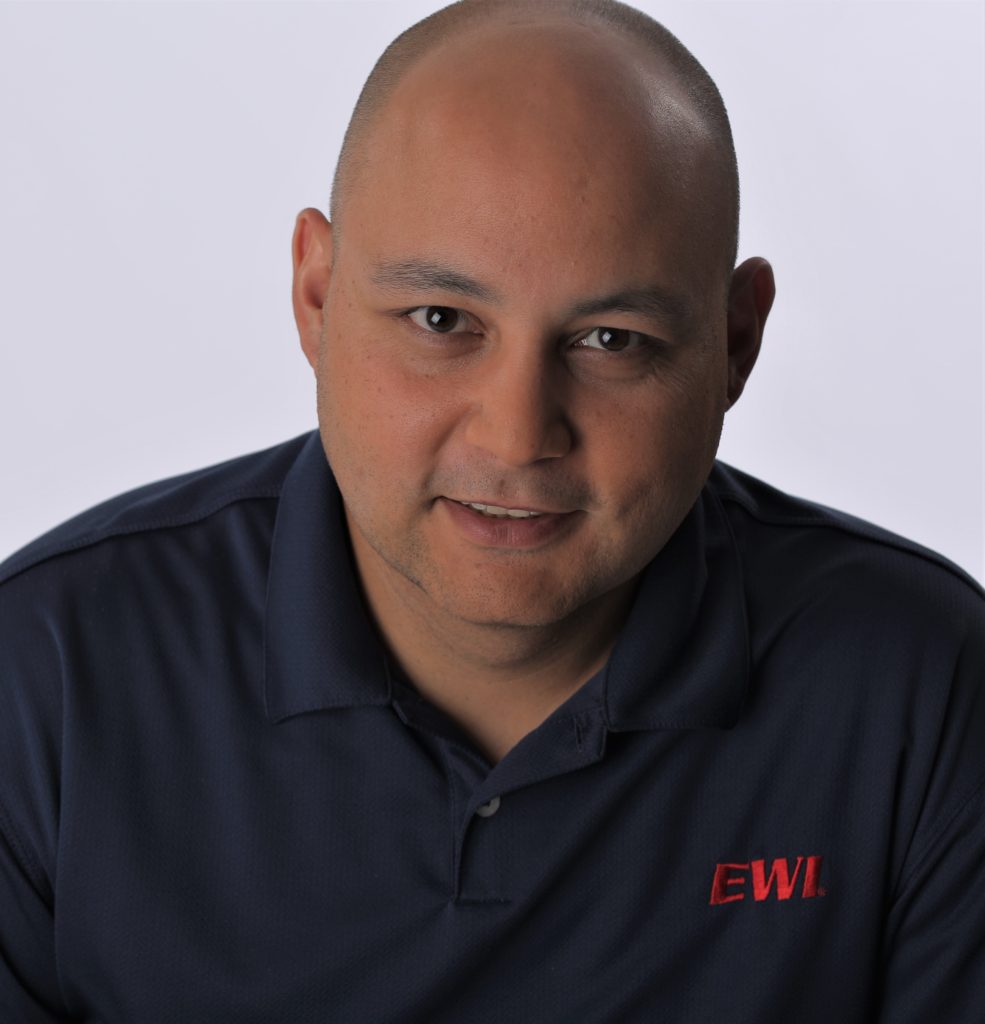
EWI has approximately 250 member companies and hundreds of other clients whom we work with periodically. I visit dozens of those customers throughout the course of a year. Some of my contacts are in the R&D group of an organization, some are in the manufacturing segment, and some are in overarching roles that go by titles such as “corporate welding engineer” or “company quality manager.” When I meet with them, I love getting into the details of their organization.
One question I ask in some form on every visit is, “How well do you coordinate work between departments?”
“Not very well,” is almost always the response.
In today’s manufacturing environment, lean manufacturing helps optimize for the best possible customer part while driving towards zero waste. There are thousands of articles written on strategies and methods to ensure lean practices in organizations. That’s why it still surprises me, as I talk to customer after customer, to hear stories about huge opportunities lost due to the lack of communication between plants/divisions/departments, resulting in duplicated effort and excess cost.
Frequently, I talk to several individuals in different departments of the same company and get asked the same technical questions from each one. EWI is often asked to do equivalent (or very similar) research for different departments or divisions within a company. In some very specific cases, this is intentional siloing for confidentiality or focus purposes. More often, though, it is a result of a host of other issues ranging from imperfect assimilation of acquired divisions to deliberate hoarding of knowledge.
Companies and researchers know this problem exists, and some have tried to solve it with variations of dotted-line matrices or centers of excellence or subject-matter working groups. Unfortunately, these “org chart” entities do little to truly tie together common challenges and drive towards a bigger goal. Usually, it’s the fact that these working group members only have collaboration as a “part-time” assignment – meaning it gets a day’s worth of attention right before the next “working group meeting”. Sometimes, it’s a matter of self-preservation, with each division reticent to share information that makes them feel invaluable.
As an independent, cross-disciplinary engineering services provider, EWI is well-suited to help navigate the difficult landscape of establishing and maintaining relationships between departments within organizations. With broad industrial knowledge, technical expertise, a manufacturing process orientation, and an array of engineering services, our specialists are able to “link the silos” so your company can get the most from its own resources. Whether it is leading a joint design review between manufacturing and research arms of an organization, identifying strengths and obstacles with an eye toward innovation, or providing staff training to help reduce the fear of new technology implementation, we have a strong track record of successfully breaking down barriers – both technical and organizational – to enable companies to reach their goals.
If you feel your organization is facing some of these internal challenges, especially as they relate to the introduction of new technologies/processes into your manufacturing environment, I encourage you to reach out to EWI. We welcome the opportunity to help bridge the gap between segments of your business and hope to serve you in this capacity.
James Cruz is a Senior Technology Advisor at EWI. He can be reached at [email protected].