
In sheet metal stamping, material property variations between batches of an incoming coil can significantly affect part quality and increase scrap rate. This issue is far more pronounced for emerging third generation (Gen III) high-strength steels. Because there are batch discrepancies, major automotive OEMs and tier 1 suppliers are interested in both real-time measurement and capability methods for predicting mechanical properties of material used in several thousand coils annually processed in stamping production lines. The measured coil properties aid in stamping process control, and predictive models are useful in the product design stage for understanding the challenges of batch-to-batch variation.
Since early 2017, the EWI Forming Center has been using a micro-magnetic material characterization system to inspect incoming sheet material properties. This system examines the interrelationship among microstructure, magnetic properties, and mechanical properties, as seen in Figure 1.
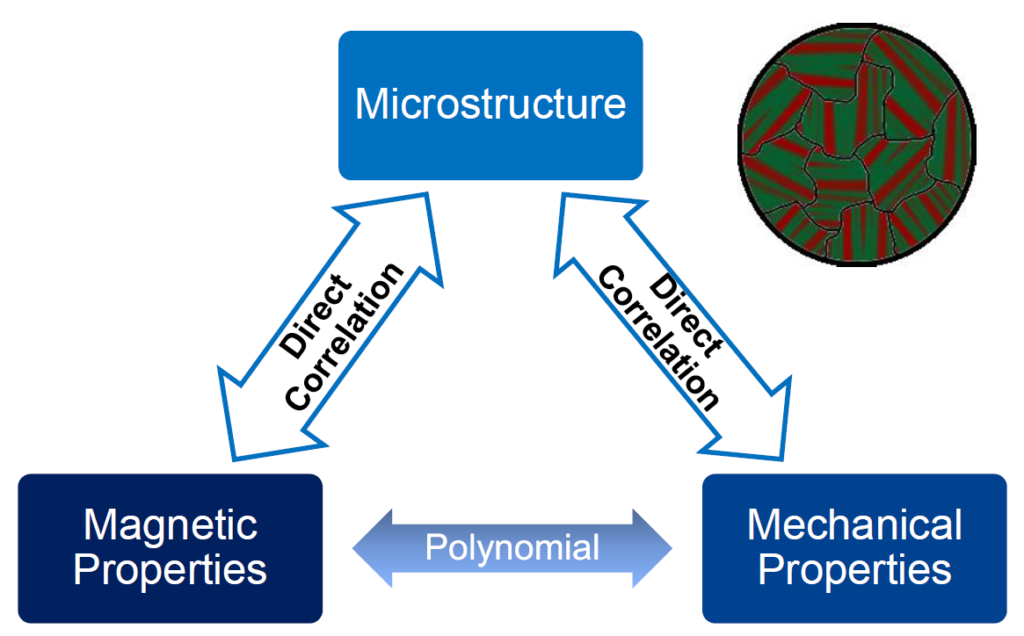
When the microstructure varies from batch to batch, both magnetic properties and mechanical properties change. While most mechanical properties need destructive testing such as hardness testing and tensile testing, magnetic properties can be measured nondestructively. With this micro-magnetic material testing method, mechanical properties are identified nondestructively using the polynomial equations of the measured magnetic properties. This nondestructive testing (NDT) system is successfully implemented in stamping production lines.
Figure 2 shows an example application of this system to monitor the yield strength variation of steel strips from a single coil in the stamping facility. The EWI Forming Center and industry partners are applying this NDT system to establish a machine-learning based algorithm for forming process control.
If you are interested in learning more about EWI’s capabilities and offerings in this area, please contact Hyunok Kim at [email protected].