
Robotic arc directed energy deposition (DED) additive manufacturing (AM) offers maximum build volume for building structures, adding features to structures, and repairing structures. The technical requirements for metal DED builds are similar to welding requirements. For example, the pending NAVSEA Technical Publication – Process Requirements for Metal Directed Energy Deposition Additive Manufacturing1 will specify maximum interpass temperature for depositing beads on builds. If above the interpass requirement, the deposition process is suspended until the build is below the temperature requirement. Metal fusion DED (wire arc, wire laser, powder laser) processes have high heat inputs and high deposition rates. Depending on the build thermal conditions, the build rate and economics will be impacted by interpass temperature requirements.
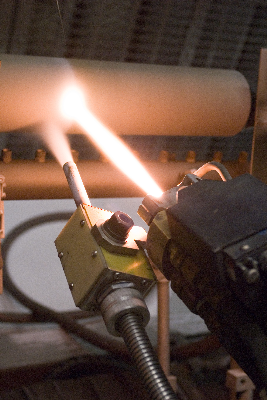
Thermal spray with LN cryogenic cooling technology used to control interpass temperature and improve duty cycle (© Air Products. Used with permission.)
On recent builds at EWI, up to 80% of build time was spent waiting for the build to cool between deposit passes. Forced air or water spray cooling can be used but both have limitations for DED AM applications. A more efficient approach is the use of cryogenic cooling for either interpass cooling between deposits or in-situ cooling directly behind the torch for maximum duty. Cryogenic cooling technology is commercially available from Air Products, which recently consigned a system to EWI for developing in-situ liquid nitrogen cryogenic cooling (ILNCC) for robotic DED processes. The Air Products’ system can vary LN flow and phase (liquid, liquid-gas, or gas) using infrared sensor feedback to control interpass temperature.
ILNCC has the potential to address two key challenges in DED AM technology: low productivity due to long wait times for cooling to interpass temperature, and high residual stresses in large deposits. It also has the potential for developing high temperature cooling rate control and providing builds with uniform isotropic properties. If interested in exploring this technology for your DED applications, please contact Dennis Harwig, Technology Senior Leader at [email protected]
- D.D Harwig, W. Mohr, S. Hovanec, J. Rettaliata, R. Hayleck, E Handler, and J.Farren, “Tech Pub Qualification Scheme Development for Arc Directed Energy Deposition Additive Manufacturing,” In Proceedings of the Ground Vehicle Systems Engineering and Technology Symposium (GVSETS), NDIA, Novi, MI, Aug. 13-15, 2019.