
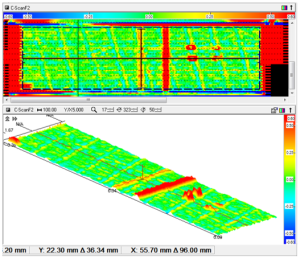
An EWI innovation team has successfully developed, integrated, and demonstrated a prototype electromagnetic/eddy current (EC) system for layer-by-layer monitoring of metal additive manufacturing (AM) processes. This system can be adapted to monitor any metal AM process where the material is deposited using a layer-by-layer technique. This technology was developed as part of a research effort to demonstrate the application of electromagnetic and eddy current techniques at all fabrication stages of AM, including (1) evaluation of feedstock (e.g. powder), (2) real-time monitoring during fabrication, and (3) post-process examination of built parts. The demonstration was conducted using EWI’s open-architecture laser powder bed fusion (L-PBF) AM test bed, which was built with funding from the National Institute of Standards and Technology (NIST) to develop, optimize, and test new techniques and tools for real-time process monitoring of L-PBF.
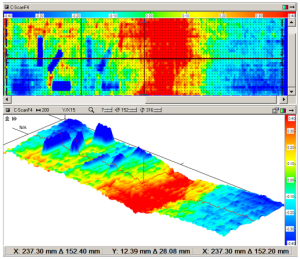
During the demonstration, process parameters were changed to create discontinuities within the build structure. The system reliably detected and imaged intended and unintended discontinuities and irregular surface conditions using a layer-by-layer approach. Subsurface discontinuities were also detected. This technology has great potential for the development and implementation of real-time AM process control.
To learn more, contact [email protected] or contact us online.