
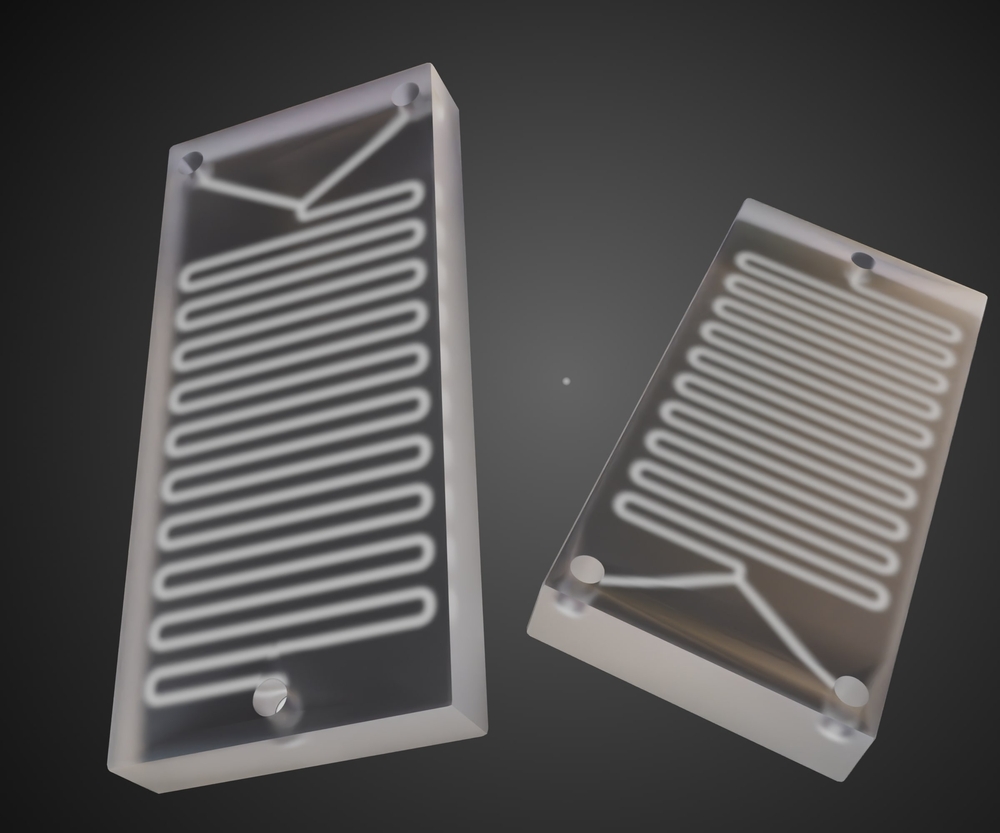
Optically transparent medical testing devices, such as microfluidic chips and diagnostic components, require precise and delicate welding techniques to maintain their functionality and integrity. The need for clarity and the intolerance of contaminates make most welding approaches unsuitable.
Hot plate welding is too imprecise due to the need to move the parts during the joining process. Vibration welding generates unacceptable particulate. Ultrasonic welding is likely to create loose flash and is also challenging to achieve strength over larger areas. Infrared (IR) wavelengths are not absorbed by polymers, which makes the IR welding process unsuited for welding transparent unfilled plastics. This same limitation prevents standard one-micron wavelength laser welding from being a viable option. Other potential welding processes, such as diffusion welding, can require long cycle times.
There is, however, one welding process that accommodates the application perfectly: Two-micron laser welding offers superior absorption characteristics in transparent polymers commonly used for medical devices like polycarbonate (PC), cyclic olefin copolymer (COC) and polymethyl methacrylate (PMMA). Due to the absorption coefficient of unfilled polymers at the two-micron wavelength, it provides efficient energy transfer and precise welding without causing excessive heat damage or distortion.
In general, the focused energy delivery of laser welding is particularly advantageous when working with intricate microstructures and tiny components typical in medical testing devices. By precisely targeting the weld zone, the laser has minimal impact on adjacent areas, preserving optical clarity and structural integrity in the product material. Furthermore, two-micron laser absorbs in most glass materials, which means it can be used to join polymers to glass as well, opening up a variety of new options. This flexibility is highly advantageous for manufacturing complex medical devices where multiple materials are often integrated to achieve specific functionalities.
Overall, laser welding using two-micron wavelength is the preferred choice for welding optically transparent medical testing devices due to its exceptional absorption characteristics, precision control, material versatility, and non-invasive nature. By harnessing the power of this advanced joining technology, manufacturers can produce high-quality medical devices that meet the requirements of transparency and reliability.
For more information about welding transparent materials, contact Miranda Marcus, Senior Engineer, at [email protected].