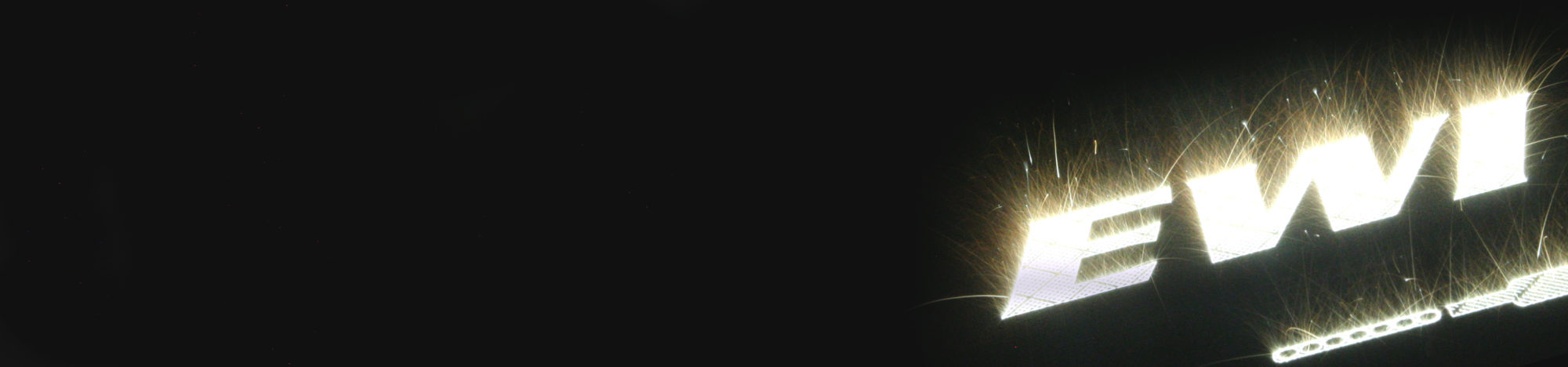
Additive Manufacturing Consortium
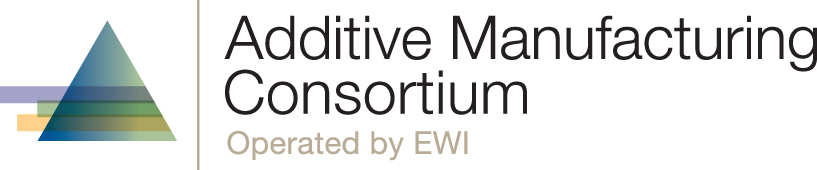
EWI established the AMC in 2010 to accelerate and advance the manufacturing readiness of metal additive manufacturing technology.
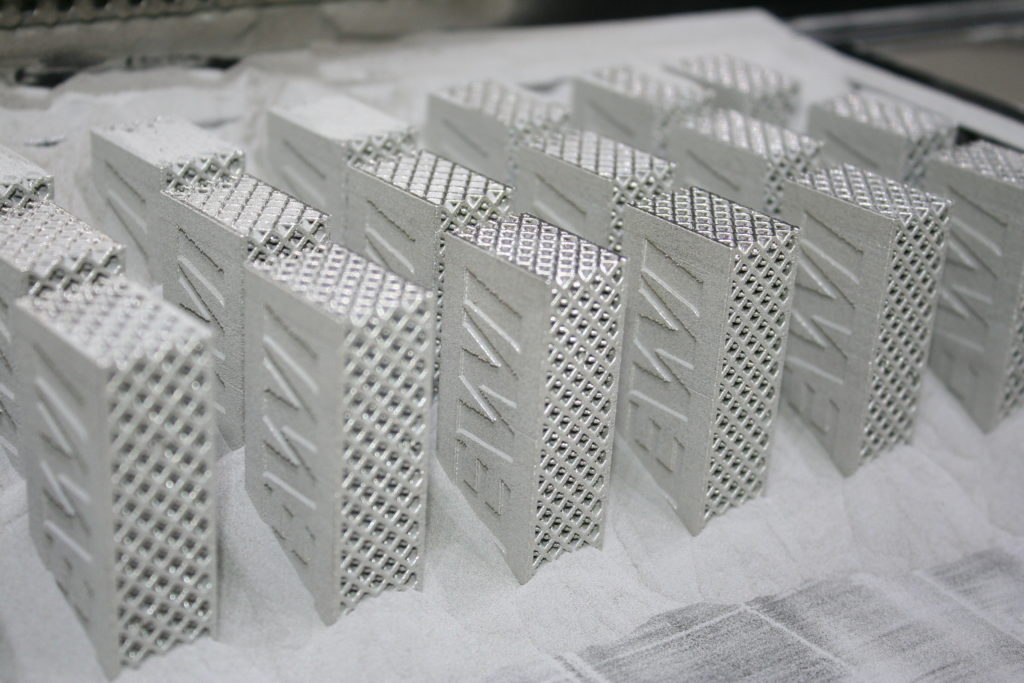
Goals
The AMC brings together a diverse group of additive manufacturing (AM) end users, suppliers, researchers, and stakeholders from across the nation to positively impact the AM landscape through organized and focused activities. The four aims of the consortia are to:
- To be a platform for collaboration across global industry, academia, and government entities
- To execute group sponsored pre-competitive AM research projects
- To partner on government funding opportunities
- To provide a forum for discussion and networking among AM professionals
Technical Focus
The AMC addresses the technical challenges in advancing additive manufacturing processes such as powder bed fusion and directed energy deposition using lasers, arc, and electron beams, as well as solid state processes such as ultrasonic additive manufacturing.
Members have access to results from previous AMC projects, including:
- Evaluation of Post Process Techniques for AM
- In-Process Monitoring & Defect Rectification: Phase II
- Testing on Current Projects IN 625 and IN 718 and Relating Microstructure to AM Properties
- DED Multi-material/ Repair
- Comparison of Commercially Available AM Simulation Tool
- Stainless Steel Multi-Process AM
Current Projects
The AMC project portfolio is funded annually by more than $2 million in cash and in-kind investments from its members. Projects in 2025 include:
- Phase 2 Faster L-PBF Consolidation Rates via High-Powered Lasers
- Phase 3 Post Finishing Evaluation and Powder Removal Verification Techniques
- Additive Manufacturing of High Entropy Alloys
- Alternative Alloys to Ti64 for both Powder and Wire Titanium Metal Additives
The results of projects are reported at AMC meetings.
Activities
The cornerstone of the consortium is technical discussion and advancement surrounding AM. Members, partners, and invited guests meet quarterly to discuss AM topics. Meetings consist of technical talks, tours, and informal social events to encourage extended conversation and promote collaboration.
Membership
Consortium members come from industry, government, academic and non-profit research organizations.
Exclusive invitation to meetings
Access to technical presentations and development activities
Non-exclusive license to joint intellectual property developed under the AMC.
Members who fund or contribute to a project receive direct access to all data and more frequent updates to project results.
The results of projects are reported quarterly at AMC meetings. In addition, all members are encouraged to present results of other, non-AMC sponsored AM activities, to promote technical interchange. Finally, government and university research partners are available to participate on AMC projects.
To learn more about joining the AMC, contact Howie Marotto, AM Business Director,, at [email protected] or 614.688.5096.
For more information about EWI’s additive manufacturing capabilities, click here.
Membership
An annual membership is required to participate in AMC meetings. Currently, the consortium has more than 50 members worldwide including aerospace and heavy equipment manufacturers; powder, equipment, and technical service providers; R&D organizations; government agencies; and academic institutions.
The next meeting of the AMC will be in Spring/Summer 2025, date TBA. For details about the meeting or for information on how to join the Additive Manufacturing Consortium, contact Howie Marotto at [email protected].