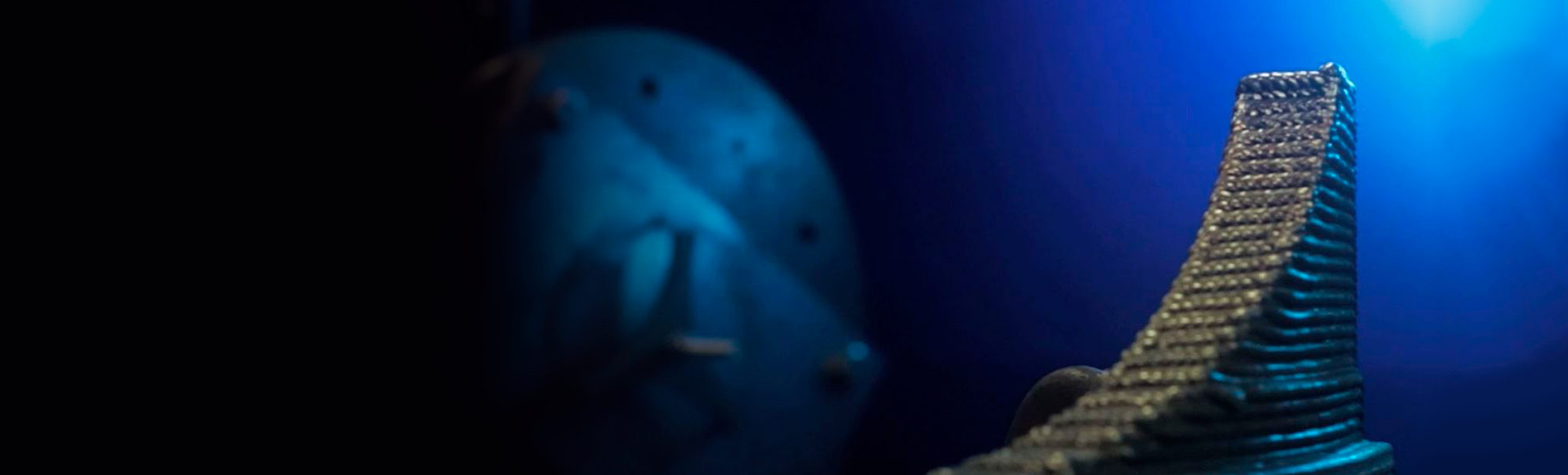
Powder bed fusion is a method of additive manufacturing that uses either a laser or electron beam to melt and fuse material powder together to develop products or parts. Powder bed fusion creates three-dimensional parts one layer at a time using a powder that is stirred or melted with one of the two types of heat sources mentioned above.
Pros of Powder Bed Fusion
- Powder bed fusion can be less expensive than other types of additive manufacturing.
- You can create models or prototypes with this type of additive manufacturing.
- It works with a variety and range of materials.
- The powder used acts as a support structure.
- The process creates less waste and is more efficient.
The Two Types of Powder Bed Fusion
There are two main types of powder bed fusion additive manufacturing. The main differences between the two are the heat sources used to melt the powder.
Take a deeper look into laser and electron beam powder bed fusion:
1. Laser Powder Bed Fusion
In laser powder bed fusion, a laser heats powdered material into parts and products. After a layer of powder has been indexed down, a new layer of powder is spread to continue the process. Ultimately, this type of powder bed fusion does not require support structures, which is what makes it unique. Without support structure, more materials are needed, which makes the process less efficient and more expensive than if you were to have a support structure.
2. Electron Beam Powder Bed Fusion
This type of powder bed fusion uses an electron beam to melt particles together and can be used with metals to create parts. It is a fusion-based technology that requires powder to be rolled on after each layer.
Powder Bed Fusion Experts
Whether you need help identifying the right process for your application or improving your existing powder bed fusion technology, EWI is here to help. Our team of experts work closely with your team to identify, develop and implement new technology within your workflow. Give us a call at 614.688.5000 or fill out a contact form.