
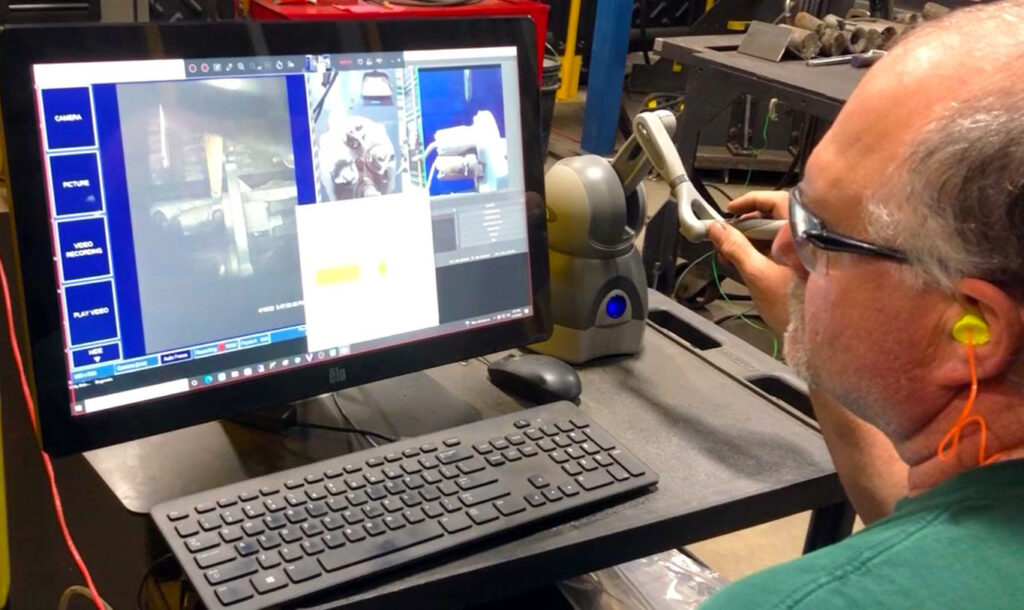
Building upon the success of our novel tele-manufacturing prototype systems, EWI has been hard at work on another innovation: tele-gouging. A direct outgrowth of tele-welding, tele-gouging is like shielded metal arc welding (SMAW) but with the addition of 80-100 psi of pressure at the torch to blow away molten metal. Due to the high pressure, the gouging process is especially loud and violent which is highly uncomfortable and potentially hazardous for the operator performing it. In addition, gouging can use as much as 1300 amps compared to SMAW which uses 400 amps or less. This creates a bigger and brighter arc, more heat, and more physical risk for the worker.
Gouging is commonly applied in steel and casting foundries. It is useful for removing substantial amounts of material very quickly. However, the standard gouging method is an intense and exhausting process to perform. Some metals have particulates that require the welder to wear a respirator as well as the standard protective welding gear (cotton/leather jacket, welding helmet, and gloves). This gear is heavy and hot, so an operator cannot endure gouging for long. The tele-gouging solution eliminates the problem of physical danger to the operator and lengthens the time that gouging can be performed by providing a system that enables remote gouging from a safer and more physically tolerable environment.
EWI’s work on developing a tele-gouging system began in late 2021 with funding from Steel Founders’ Society of America (SFSA). EWI took the knowledge gained from its previous tele-welding projects and has applied it to tele-gouging. Using a haptic stylus, an operator sitting at a desk in a remote welding station operates a robot. Like SMAW, a gouging electrode is consumed during the process, thus continually decreasing the distance between the gouging torch and the part. Unlike in tele-welding, a tele-gouging operator can run out of downward movement on the stylus, making it difficult to perform a free-form simulation of gouging movements.
EWI has tackled this challenge by giving the user the option to lock in a constant feed rate on the robot (the feed rate being the time it takes for the electrode to get burned up), which is automated on the feed rate axis. With a stabilized feed rate set by the operator, the robot maintains control on the one axis while the user is free to control of all the other axes. A few cameras in the welding booth and on the robot provide the live view for the operator, who can view the monitor on a desktop PC while remotely controlling the gouging process located out in the shop. To view the process in action, click here.
EWI has demonstrated the system to casting foundries and can customize the tele-gouging system to fit the foundry’s needs. In addition to tele-gouging, EWI is continuing to explore other manufacturing processes to adapt for tele-manufacturing including tele-grinding and SMAW.
If you want to learn more about tele-gouging or other tele-manufacturing work being conducted by EWI, contact Connie LaMorte at [email protected].
Acknowledgment: This research is sponsored by the DLA-Troop Support, Philadelphia, PA, and the Defense Logistics Agency Information Operations, J68, Research & Development, Ft. Belvoir, VA