
Each year, EWI associates nominate their peers for the annual Technical Excellence Awards. We are pleased to announce three award winners this year – two engineers and one technician – all of whom have made outstanding contributions in applied R&D and new services for EWI clients.
Olga Eliseeva, Project Engineer
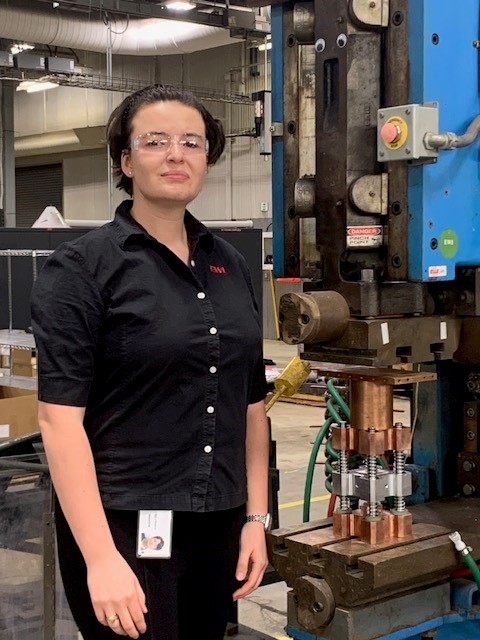
EWI has pioneered a groundbreaking new process for solidifying metal powder called resistance-based sintering. The technique produces fully consolidated parts with limited-to-no porosity and no sign of internal oxidation. This improved powder consolidation method can be used in place of die casting, metal injection molding, and hot isostatic pressing. Further, unique new material combinations can be produced through this method. The leading research engineer for resistance-based sintering has been Olga Eliseeva. Olga joined the EWI resistance and solid-state group in 2021 after earning her Ph.D. from Texas A&M and has been a crucial player in both internal and client-based R&D since then. Her engineering experience and interests are broad, and over the past two years her work has involved resistance welding, design of experiments, data science, and additive manufacturing. In the past year, Olga has presented at numerous professional events, including MS&T, the AWS Professional Program at FABTECH, the Turbine Forum, and the ASSEMBLY Show. She was a featured guest earlier this year on the ASSEMBLY AUDIBLE podcast and was highlighted in the May/June issue of Advanced Materials and Processes.
Jesse Rhodes, Application Engineer
If you are a follower of EWI activity, you have seen a lot about the emerging hydrogen economy and our commitment to addressing the safety issues related to H2 transmission, distribution, and end-use systems. A key initiative in the past year has been to develop a robust framework for conducting extensive mechanical and metallurgical property testing on pipe steels and associated pipeline welds under a variety of hydrogen exposure scenarios. Jesse Rhodes, a member of our structural integrity group since 2021, has been the primary designer of EWI’s system for high-pressure H2 environment testing and serves as the lead engineer in our state-of-the-art hydrogen testing labs. Construction of the labs began in in May of 2022, and they officially opened to commercial activity in January. To address the challenges of conducting sophisticated tests in high-pressure hydrogen environments, Jesse designed a direct current potential drop (DCPD) system and an optimized pull rod sliding seal. He has also been involved in several internal research projects, and recently wrote a paper, Required Soaking Time for Hydrogen Testing. Jesse presented EWI’s work at the ISOPE meeting in Ottawa last month.
Kevin Collins, Senior Technician
Standing up two brand-new, pressurized environmental testing labs with seven servo-electric test frames, 24 pressure vessels, a DCPD system, a glovebox, an oxygen analyzer, and all the accompanying alarm, sensor, and ventilation systems is not a one-man job! Getting the hydrogen lab outfitted and operational in less than a year couldn’t have been achieved without the efforts of Kevin Collins, technician extraordinaire. Kevin came to EWI with experience in pipeline fracture, fatigue, and corrosion testing, having served for several years as an environmental engineering technician. He joined us in 2022 just as the equipment for the H2 lab started rolling through our doors. He has since worked tirelessly to integrate new machines into our labs safely and efficiently. Today, both set ups are fully functional, performing tests including slow strain rate, ASME B31.12 – KIEAC/KIH fracture toughness, actively-loaded fracture toughness, and fatigue crack growth rate measurement and S/N fatigue evaluation. To see the EWI offerings made possible by Kevin’s work, take a look at Materials Evaluation for Hydrogen Infrastructure.
Congratulations to these three talented EWI associates!