
Directed energy deposition (DED), which leverages commercial robotic welding systems, is an agile and economical large-scale additive manufacturing (AM) process. DED AM is low risk since it leverages existing welding process equipment, consumables, procedures, and standards – which all have decades of proven performance. Using DED “digital” computer-aided manufacturing (CAM) software, component structures can be additively manufactured, welded, cladded, or repaired utilizing solvers that automate robotic path plans. Robotic CAM software makes high-mix/low-volume applications affordable. It also enables multi-process digital manufacturing in which welding, AM, and metalworking (milling, grinding) can be combined into “lights-out” applications. To achieve this manufacturing advantage, a “digital twin” must be set up of the robotic system and carefully calibrated to the physical system for robust operations. Once the digital twin is developed, most DED AM equipment suppliers will offer a “pre-engineered” system to recover their system development costs over many units and provide better value to industry.
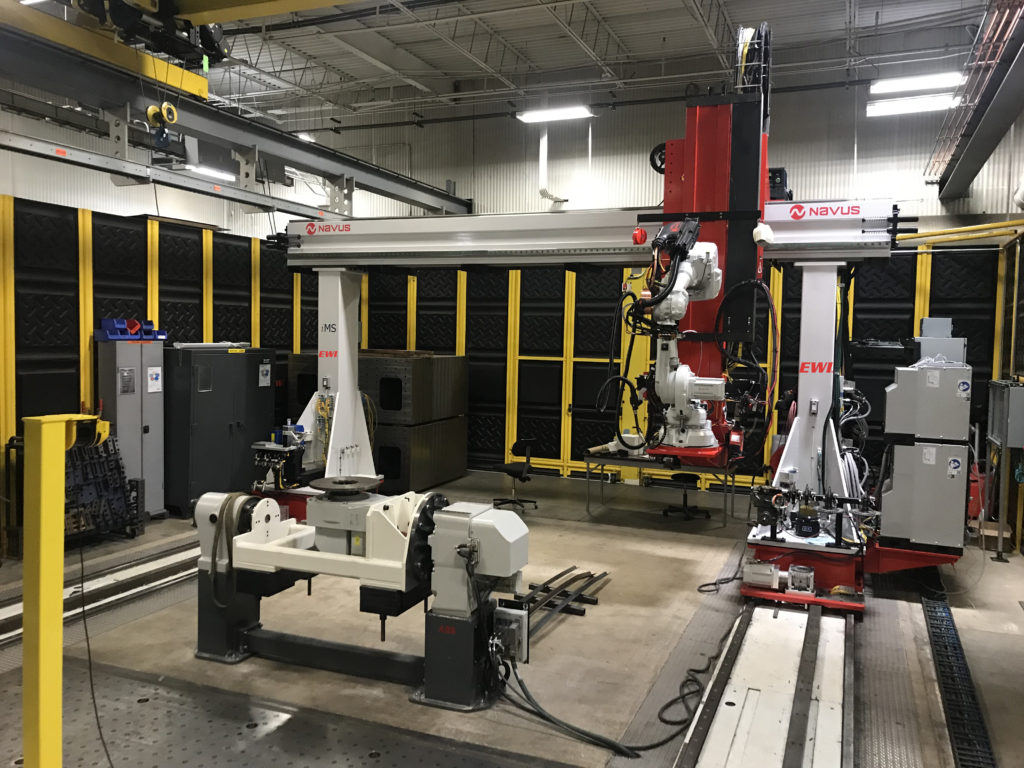
Due to the complexity of existing DED software, the range of commercial robotic DED systems available has been limited. EWI’s arc welding & DED processes team has been busy over the last two years transforming EWI’s robotic welding laboratory into a “digital” robotic manufacturing laboratory. Six commercial robotic systems have been modeled in Autodesk PowerMill CAM software, and new equipment like Cloos Robotics’ multi-process system are in progress. Each robotic system has a digital twin and post-processor that have been calibrated to ensure precise CAD-to-path deposition performance. These range from 7- and 8- axis systems for single and double-sided builds to a duel-robot 14-axis system for multi-process applications to our new Navus robotic gantry DED system which offers the largest metal DED-build capacity available in North America for application development.
As an example, the Motoman 7-axis DED system (Figure 1) is equipped with a Fronius TPS 500i welding package. It is used for both single-sided and double-sided build platform builds using a head and tail stock positioner. The Motoman DED system was used in a National Shipbuilding Research Program (NSRP) project to make a commercial ASME steel pipe coupler and nickel-aluminum-bronze high-pitch propeller blade.
EWI’s robotic DED lab also includes two OTC Daihen 8-axis systems, a 6-axis Fanuc system, a 14-axis Genesis duel-arm Fanuc system, and the Navus multi-process 11-axis ABB robotic gantry system (Figure 3). This gantry system offers an extra-large build volume of 8-10’ high (depending on ceiling conditions) x 14’ wide x 30’ long. Other features include a 60-kg arm capacity, an ATI tool changer, and a diverse sensor package for quality, thermal, and dimensional management. The ATI tool changer can be used to switch between deposition apparatus (arc to laser to hybrid laser arc equipment) and metalworking apparatus (a 5-hp spindle with grinding, brushing, and burring capabilities). The system offers a 2-axis 1-ton tilt/turn positioner for single- and double-sided builds, as well as a Binzel neck-changer and maintenance station to support lights-out build conditions.
EWI is focused on improving the economics of robotic DED systems for large-scale structures. This technology can be used to replace large-scale castings, build complex structures and much more. Please contact Dennis Harwig at [email protected] or Michael Carney at [email protected] to explore the potential for your structure manufacturing needs.
For a more detailed look at EWI’s recent arc DED research, click here.