
EWI and Sciaky will work together to 3D-print metal prototype parts for a wide range of manufacturers
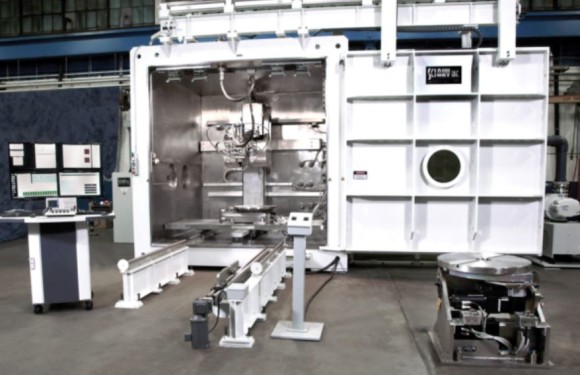
EWI, a leading engineering and technology organization dedicated to developing, testing, and implementing advanced manufacturing technologies has purchased an industry-leading Electron Beam Additive Manufacturing (EBAM™) system from Sciaky, Inc., a subsidiary of Phillips Service Industries, Inc. (PSI), and leading provider of metal additive manufacturing (AM) solutions.
The Sciaky EBAM-110 system purchased by EWI is an electron-beam, wire-fed, direct energy deposit machine for additively manufacturing large parts. (The process is EB-DED, “electron beam direct energy deposit”). The industry-leading system is capable of delivering a lot of material fast, which gives it an advantage over several other AM processes and makes it especially applicable to creating parts for the aerospace and space exploration sectors.
EWI and Sciaky have entered into an agreement to work together to “identify mutually beneficial collaborative commercial and government projects that utilize the strengths of both organizations to advance EB-DED state of the art” for clients including government-funded, joint-industry, and single-sponsor projects.
As the most widely scalable, metal 3D printing solution in the industry (in terms of work envelope), Sciaky’s EBAM systems can produce parts ranging from 8 inches (203 mm) to 19 feet (5.79 meters) in length, but can also manufacture smaller and larger parts, depending on the application. EBAM is also the fastest deposition process in the metal additive manufacturing market, with gross deposition rates ranging from 7 to 20 lbs. (3.18 to 9.07 kg) of metal per hour. Plus, with a dual wirefeed option, two different metal alloys can be combined into a single melt pool to create “custom alloy” parts or ingots. In addition, the mixture ratio of the two materials can be changed to create “graded” parts or structures.
The system is due to be installed at EWI’s Buffalo Manufacturing Works facility by the end of the calendar year.