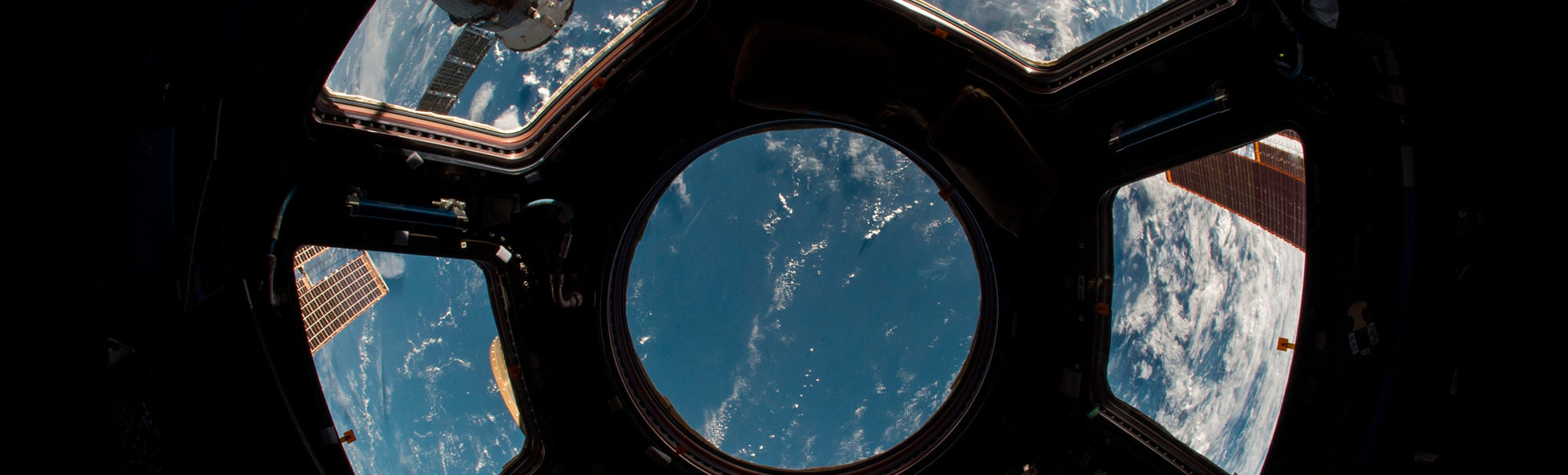
Aerospace
Space exploration is on the rise, and commercial aviation is on the rebound. Advanced aerospace manufacturing technology and processes will play a key role in driving efficiency throughout the supply chain.
As an applied engineering research and development organization, EWI delivers aerospace engineering services to solve tough problems. We help organizations meet requirements for space exploration, civil aviation, and air defense as they incorporate or develop new aerospace technologies and improve production and testing.
Aerospace Manufacturing Solutions
For decades, EWI has been recognized as a national leader in technology advancements and new product R&D for the aerospace industry. From advanced aerospace materials testing to specialized aircraft welding, our experience is comprehensive and supported by our independent testing labs. Our customers include Northrop Grumman, Boeing, Lockheed Martin, and NASA.
Today, we are addressing important challenges like reducing time to production of new technology, developing new alloys and materials to improve flight performance, and validating solutions through rapid aerospace prototyping services. We’re also solving unique problems related to aerospace thermal management and additive manufacturing.
Whether your organization is a prime contractor or part of the supply chain, EWI will help you implement improved fabrication methods using advanced manufacturing technologies. Leaning into our broad engineering experience in advanced manufacturing techniques and processes, we’ll help your company meet your goals, stay competitive, and lead the industry into the future.
Our cross-disciplinary engineering teams are ready to integrate these critical technologies and services to support your business:
EWI Initiatives
- Advanced Welding Technologies
- Large-scale Additive Manufacturing
- Hypersonic Engineering
- Carbon and Carbon Fiber Joining
- Advanced Alloy Development
- Data Science
- Advanced Automation
- Battery and Fuel Cell Development
EWI can help you identify the right technology, develop ideal processes, and implement your innovations.
Want to learn more?
Check out EWI’s research, video demonstrations, and service overviews for the aerospace industry.