
By James Cruz, EWI
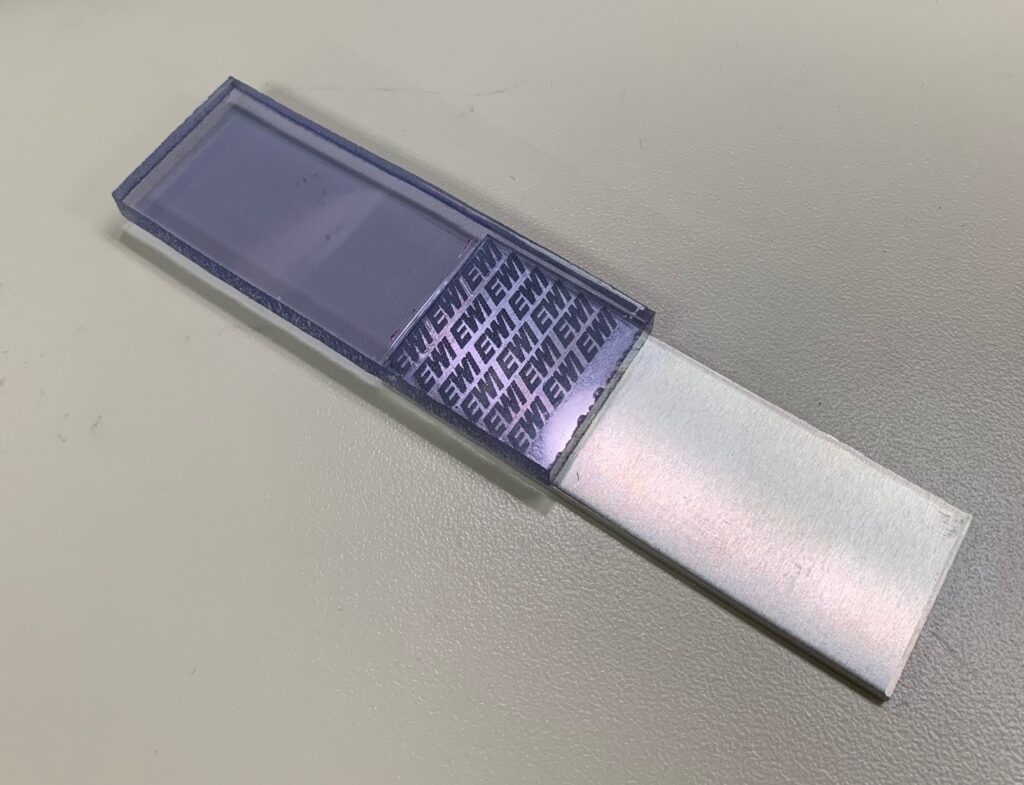
My first job out of college at Honda of America Manufacturing was a dream come true—the chance to play with robots and build cars! They handed me several crisp, white uniforms on day 1. Within that first week on the production line, however, I had soiled my pretty white pants with a huge, black, gooey streak of gunk. I had formally been introduced to one of the adhesive sealants used in automobile assembly.
Over my decade at Honda, I grew to understand what a pain adhesives can be in production, seeming so often to end up everywhere except where they’re wanted! They’re expensive and have limited shelf life. Year-in-year-out, they were one of the top reasons for downtime in my department because they coated proximity switches or clamps and caused equipment issues.
Now, I fully appreciate the value of adhesives and understand that they can significantly improve joint performance, especially when combined with welding. Adhesives for metal-to-plastic bonding can be effective. But what if the question, “What’s the best adhesive to bond plastic to metal?” is not always the right question at all? What if you had a way to use lasers for direct-joining of metal and plastic without all the side effects of adhesives?
Plastic-to-Metal Joining Methods without Adhesives
“How to join dissimilar materials” is one of the most common questions we get at EWI. In aerospace engineering applications, those tricky-to-stick materials might be Ti-6242 and Ti-5111. In medical device engineering applications, maybe Nitinol and stainless steel. In both of those industries as well as others, clients ask us about polymer-to-metal bonding because we specialize in that. At EWI, we have demonstrated the processes of direct-joining metals and plastics with incredible results.
Recently, EWI’s Senior Technology Leader for polymers, Jeff Ellis, wrote a paper about using a polymer lid on an EV battery box. While a gasket/adhesive + mechanical fastener approach would work for metal-polymer adhesion, wouldn’t it be great if we could direct-bond the lid? So, Jeff came up with two novel techniques for joining metals and polymers, both of which require little cycle time:
Method 1: Use Laser Etching
The first process for bonding metal to plastic is to laser etch the surface of the metal. EWI has optimized the process to melt microscale valleys. The melt from the valley is pushed up the edge of the valley, creating a protrusion with ends that overhang the valley. This enables a surface that is clean and has a mechanically functional topography. For the etching, we use a Laser Marking Technologies 100W 1064 nm pulsed fiber laser.
Method 2: Melt It
The second process is to melt the polymer into the functionalized metal surface. This requires both force and heat, which cause flow into the microfeatures. EWI’s engineers have used two different methods for heating with similar results. Both methods employ compression to encourage the viscous melt to fill the metallic microfeatures:
- Transmission laser heater: A 1µm continuous laser is shined through the polymer to the metal surface to heat it.
- Induction coil: The coil heats the metal and thus also the polymer at the interface.
Parts resulting from both of these methods have shown shear strengths of more than 1000 psi. Also, initial testing has produced leak-free parts when tested using an air decay method. Finally, when cycled from 0 to 65°C, the parts showed no difference in mechanical strength despite the difference in coefficient of thermal expansion between the materials.
Bond with EWI for Materials Joining Solutions
While EWI and other engineering innovators continue to investigate how to join plastic and metal, we know that methods explored so far have great possibilities for manufacturers.
EWI would love to work with you to explore applications of the exciting techniques from this article, as well as solve any other materials joining puzzles in front of you. Want to learn more? Complete our form to connect with the EWI team.