
In his blog Who Let the Frogs Out?, my colleague Marc Purslow wrote about EWI’s innovative work to automate the repair of austenitic manganese steel (AMS) frogs; the special trackwork components used by railroads to allow track to converge, diverge, or cross. In this Phase I project sponsored by the Federal Railroad Administration (FRA), EWI developed an automated flux cored arc welding (FCAW) repair process, repaired a damaged frog, and sent it to the Transportation Technology Center Inc. (TTCI) in Pueblo, CO to undergo simulated in-service testing. The performance of the repaired frog in TTCI’s test track far exceeded expectations, as it accumulated over 118 million gross tons (MGT’s) prior to scheduled removal and evaluation. Compared to baseline data, this represented a 240% increase in lifespan compared to frogs repaired using current shielded metal arc welding (SMAW) and FCAW processes, and more than a 100% increase in lifespan compared to a new, unrepaired frog. It should also be noted that the repaired frog could have stayed in track longer, if not for project scheduling and budgetary constraints. The success of this program led to an FRA-sponsored Phase II project with the goal of developing improved welding consumables, increasing overall productivity, and performing real-world testing in a heavy-haul line.
EWI began the Phase II project by developing a metal-cored gas metal arc welding (GMAW) consumable to replace the standard flux-cored consumables commonly used for current-day semi-automatic weld repairs. The goals of this development were two-fold: (1) to improve weld quality by reducing the slag inclusions inherent to the FCAW process, and (2) to increase overall productivity by decreasing the need for interpass cleaning to remove slag.
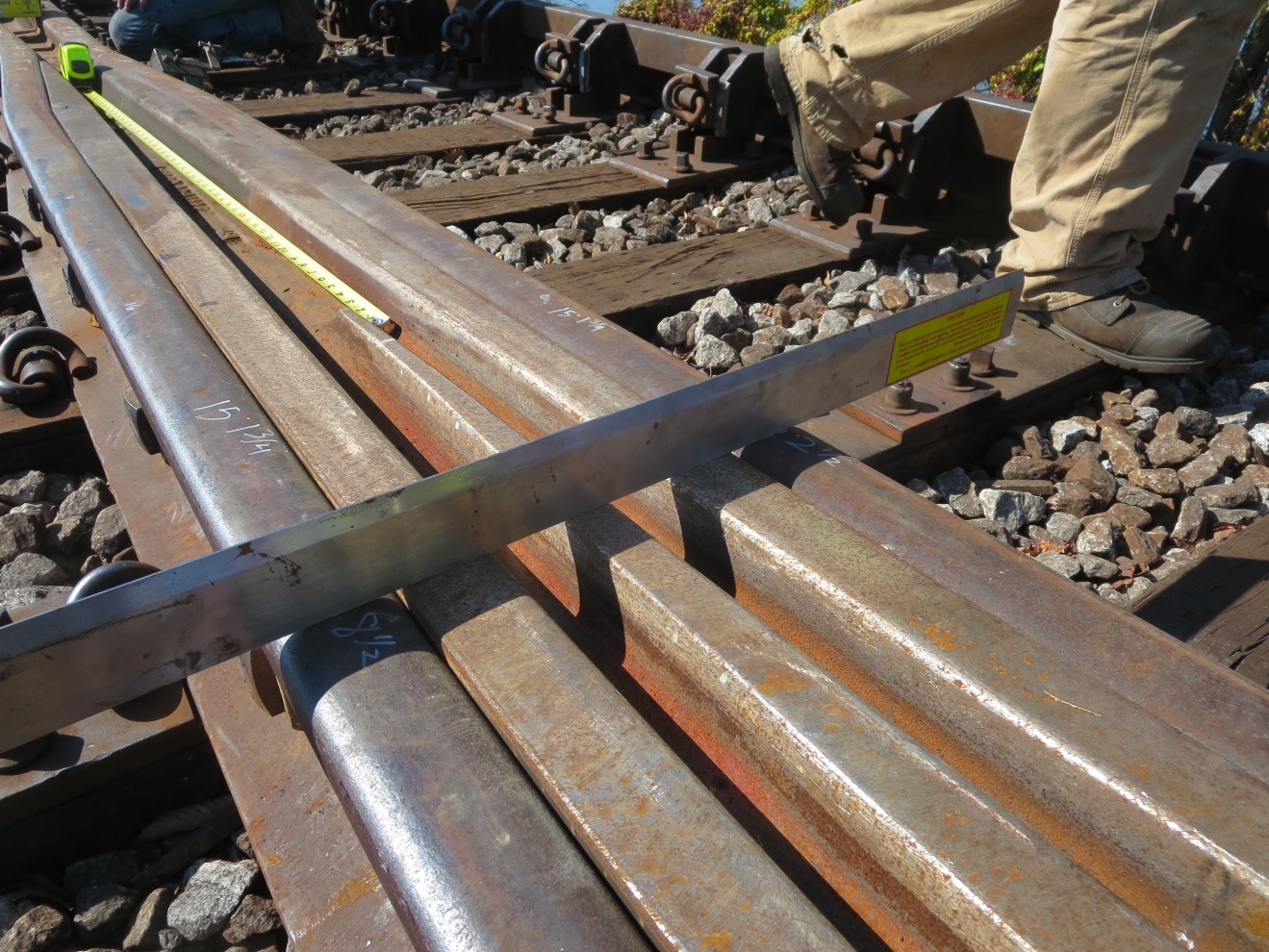
Employing many of the innovative techniques developed in the Phase I project, EWI used this new consumable to repair a worn frog donated by the CSX corporation (Figure 1). A key partner in both the Phase I and Phase II projects, the CSX corporation also agreed to test the repaired frog in revenue service on one of their heaviest haul lines in Tanner, Alabama (Figures 2 and 3). This test has been scheduled for a maximum of 18 months in service, where the repaired frog will see up to 120 MGTs. This will provide a similar durability evaluation as the test conducted at TTCI, yet in a real-world environment. Since its installation on November 1st, 2016, initial performance has matched that of the frog testing in the Phase I effort.
While the full results of this real-world test remain to be seen, this innovative approach to extending the life of the railroad industry’s most expensive track components has generated significant interest. EWI has developed multiple concepts for application of this process, both as an in-track repair offering, and as a mobile repair station that could be deployed to so-called frog ponds: the locations where worn frogs are deposited after removal from service and are awaiting repair. In the latter scenario, multiple frogs would be repaired, held in inventory, and put back into revenue service as needed.
To learn more about this innovative multi-year project, please contact [email protected] or click here.