
PROBLEM / OBJECTIVE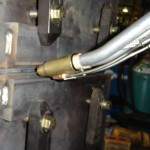
Construction of Navy ships requires an extensive amount of out-of-position (horizontal, vertical, overhead) welding of high‑strength steel joints for units, blocks, and other major structures. The majority of these erection joints are currently accomplished with gas metal arc welding (GMAW) and flux cored arc welding (FCAW) processes. Travel speeds and deposition rates are relatively low with these processes limiting productivity. The objective of this project is to develop tandem gas metal arc welding (T-GMAW) for out-of-position steel erection joints used on Navy carriers and submarines in order to increase productivity.
ACCOMPLISHMENTS / PAYOFF
Process Improvement:
Procedures for T-GMAW have been developed for high‑strength steel in the horizontal welding position. During this initial phase of process development, deposition rate improvements of over 200% were achieved while maintaining acceptable heat input levels, and weld quality. Horizontal welding procedures were also pre-qualified on high‑strength steel plate material at EWI. Similar gains have been attained for the overhead welding position. These welds have passed Level l non-destructive test procedures given in Navy technical publications. Northrop Grumman Shipbuilding -Newport News(NGSB-NN) has indicated that preliminary qualification test plates are not necessary at this time.
Implementation and Technology Transfer:
The project team is led by the Navy Joining Center (NJC) working with NGSB-NN and theNavalSurfaceWarfareCenter, Carderock Division (NSWC‑CD). During Phase III of the project, the welding procedures were further refined, and a shipyard system was leased and used by NGSB‑NN to produce preliminary qualification test plates. The NJC is supporting the shipyard with the transition and qualifications required for each welding position using the production machinery. BIW has expressed interest in the technology pending results from the program.
Expected Benefits and Warfighter Impact:
NGSB-NN will use mechanized GMAW on approximately 7,200 feet of out-of-position weld joints to fabricate the CVN-78 carrier and the SSN‑781 submarine. This represents a labor effort of approximately 30,000 man-hours. Doubling or tripling the welding deposition rate through the use of T-GMAW will result in savings of 15,000-20,000 man-hours on these two platforms.
Preliminary estimates for the horizontal welding position show a per-hull savings of $500K for CVN‑21 platforms, and $120K for the Virginia Class submarine modules fabricated at NGSB‑NN.