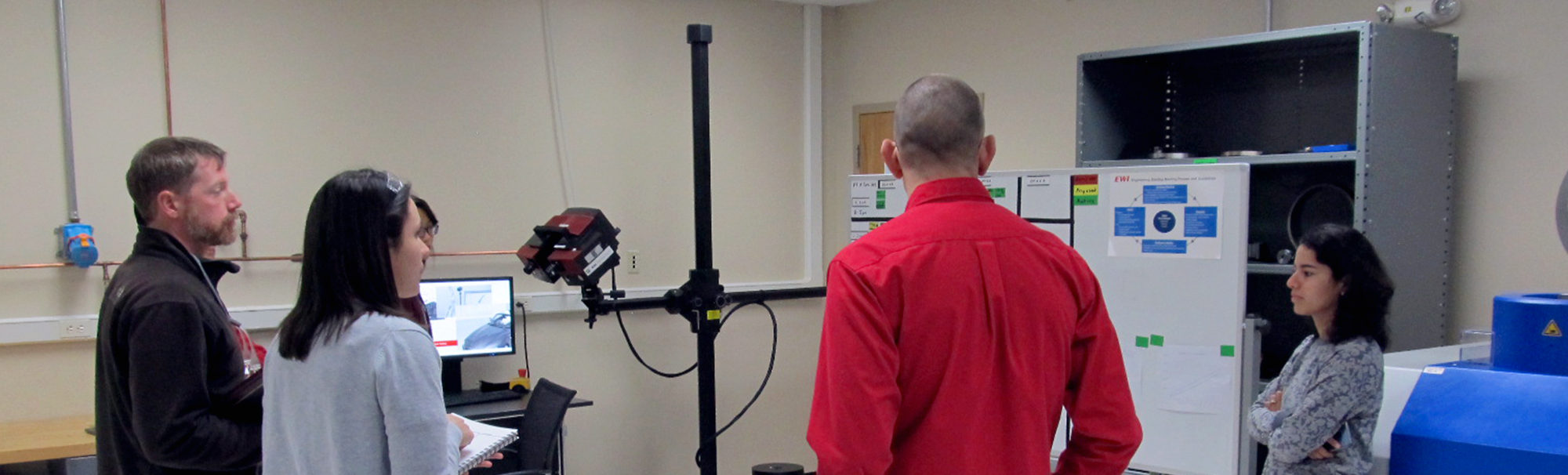
Forming
The EWI Forming Center helps organizations evaluate new forming technology so they can fully harness it for their operations.
Our advantage is twofold: We have the materials expertise and technology to test, refine, and innovate new solutions.
Advanced forming capabilities in the EWI Forming Center are supported by the following:
- 300-ton AIDA servo press
- Erichsen Universal Sheet Metal Testing Machine
- 3MA electromagnetic based NDE system
- ARGUS optical strain measurement equipment with GOM analysis software
- Digital image correlation (DIC) equipment
- Full range of stamping, incremental forming, and forging simulation tools
- Warm/hot forming test cell
- ATOS optical 3D CMM system
- UNIST automated sheet lubricator
These resources enable our engineers to determine the formability of new materials for sheet metal forming and forging processes, and to provide recommendations for materials, lubricants, coatings, and process parameters.
Why Choose EWI for Sheet Metal Forming?
The EWI Forming Center offers a range of services that are unmatched in the industry:
Pre-competitive Research
EWI operates the EWI Forming Center Consortium (FCC), which conducts precompetitive research focused on automotive forming technologies. The FCC launched in 2017 with nine founding member companies including automotive OEMs, tier one suppliers and materials producers. In addition to the projects run through the FCC, EWI has conducted a number of joint industry projects that address specific technical issues (e.g., warm-forming high-strength aluminum).
Materials Formability Evaluation
EWI’s Forming Center offers material formability testing of various types of sheet material including steel, aluminum, titanium and nickel alloys. These tests include cup draw testing, biaxial bulge testing, and FLD testing. EWI engineers evaluate the results of these tests (and others) to provide recommendations on lubricants, coatings, and materials for your specific application. View our full list of formability testing services. To speak to a specialist about EWI’s formability evaluation, call 614.668.5283.
Workshops & Training
It’s our goal to provide a training base for students and engineers. We fulfill this commitment through the Forming Center’s annual Advanced Sheet Metal Forming Technology Workshop, EWI’s two-day Fundamentals and Applications of Metal Forming Course, and regularly published newsletters. Workshops and courses are generally held at EWI’s headquarters in Columbus, Ohio. Check our current calendar for upcoming classes.
High Impact Projects
Over the years, EWI’s forming team has pushed the envelope in materials forming science and to help our clients succeed. Here’s a selection of some of our past projects:
- Designing a hot-forming process and developing a prototype Inconel 718 aerospace jet engine component
- Designing a progressive die forming process for high-volume electronic mobile devices
- Developing and applying practical failure criteria for necking failure, edge cracking, and shear fracture in computer simulations of stamped automotive parts with AHSS
- Developing a practical warm-forming process with Al 6xxx-7xxx, Niobium, and Al-Li alloys for lightweighting vehicle structures with multiple industry sponsors
- Developing a prototype electro-magnetic forming process for beverage cans and bottles
- Designing an intelligent servo-controlled forming process using machine learning
Identify.
Develop.
Implement.
WE MANUFACTURE INNOVATION.
That’s how we break through technical barriers and shape the future of sheet metal forming.
Resources at Your Service
To learn more abut our forming capabilities, contact our Forming Center team.
____________________
EWI also operates the EWI Forming Center Consortium (FCC), which provides thought leadership and conducts collaborative sponsored projects to solve common challenges in sheet metal forming. To learn more about FCC membership and activities, contact Laura Zoller at [email protected].