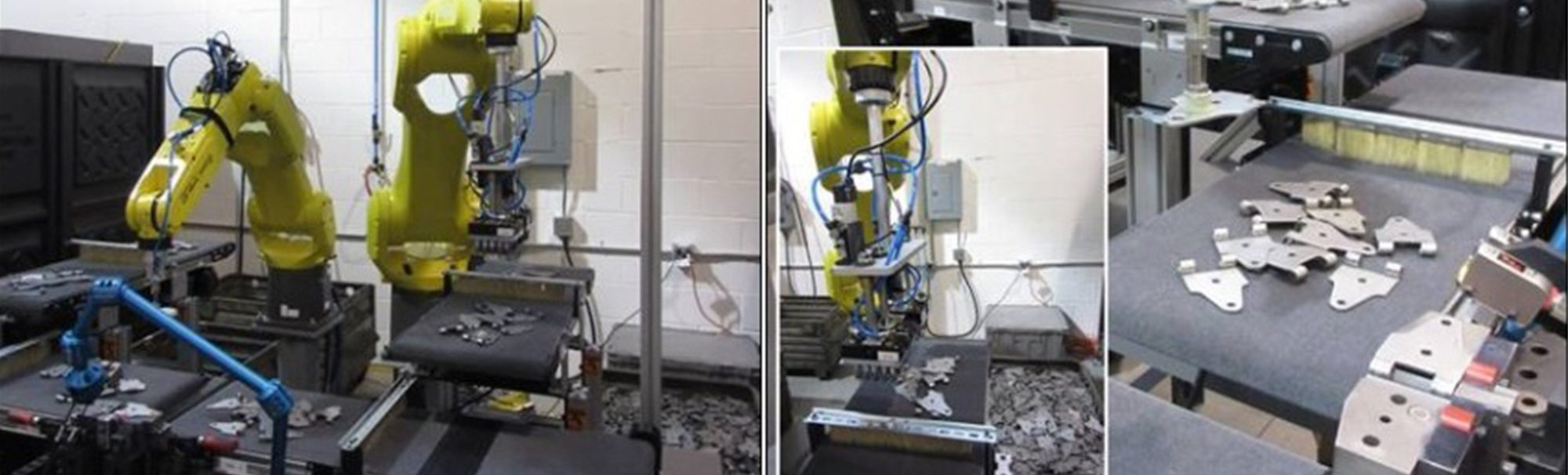
Production Support and Lab Services
Do you need an unbiased third party to assure the quality of your product to your customers?
EWI offers PRODUCTION SUPPORT to qualify your materials and processes, train your staff, and provide onsite assistance as needed to ensure high standards.
Proving the quality of your product is a crucial part of building a successful business and reputation in the marketplace. This is even more important for manufacturers, who need to meet both consumer demand and safety standards. Setting up a validated production process with guidance from manufacturing professionals can go a long way toward ensuring the satisfaction of your customers. With EWI, you have access to an array of support services to help you establish best practices for your team and in your facility.
Our specialists help
Qualify your materials
Qualify your processes
Train your production staff
Review and monitor your in-plant procedures
…So you can
Validate your parts and components
Elevate the skill level of your workers
Guarantee your deliverables
Promote your products with confidence
Production Support Resources
- Laboratory Testing Services
- Material Analysis Services in H2 and CO2 Environments
- Training & Classes
- Onsite Consultation
- In-plant Advisors
- EWI Welding Products