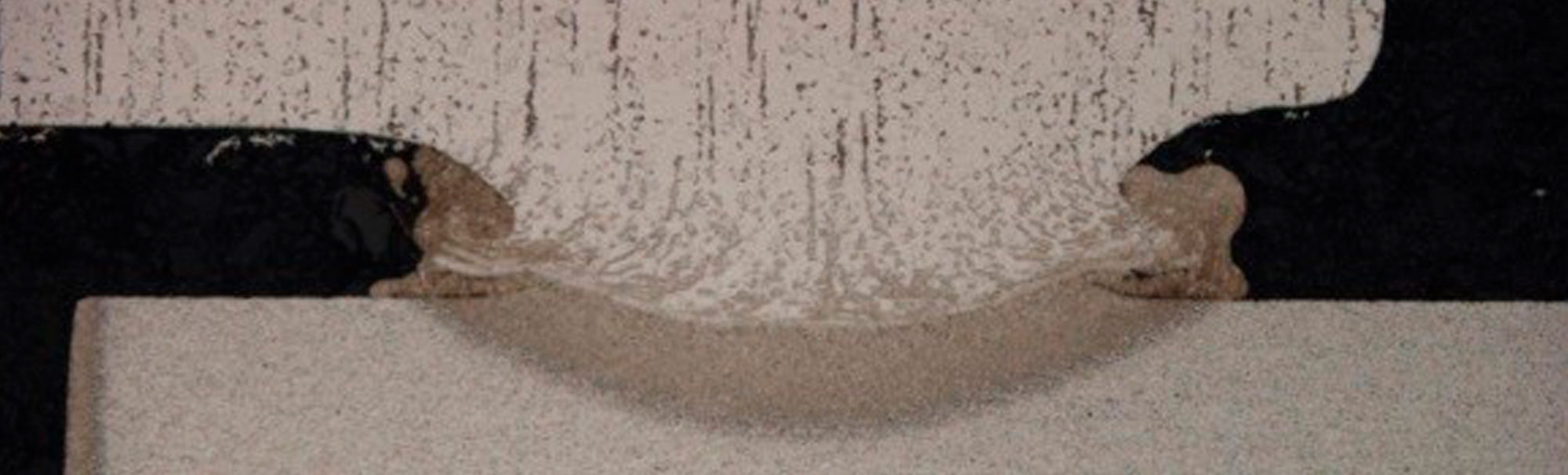
Resistance Welding & Solid-state Processes
Dissimilar metals joining is at best difficult and often impossible to achieve with traditional fusion methods.
Resistance welding and solid-state processes have proven to be the most successful in joining dissimilar materials.
EWI specializes in all types of resistance and solid-state welding. With broad expertise in materials science and controls engineering, we are able to be proactive in the face of new material joining challenges. Organizations often come to us with these goals in mind:
- Join difficult material combinations
- Develop tailored metallurgical properties, such as locally softening materials without sacrificing strength
- Develop customized repair technology
- Accomplish all goals in a timely, resource-conscious manner
Joining Solutions from a Dedicated Partner
EWI’s broad resistance and solid-state welding capabilities have made us a trusted partner for organizations in industries like automotive, aerospace, rail, and oil and gas. Much of that trust, however, comes from our ability to help throughout the development of a new production process, from tailoring technology to developing/executing design-of-experiment (DOE) methods. We use physics-based modeling to simulate conditions, set process parameters, and make sure the solution we provide is customized for the best outcome.
Our Welding Expertise in Action
EWI works to stay ahead of ever-changing market demands and technological advances. We’re proud to have developed resistance welding processes like these automotive industry examples:
- Developing in-situ heat treatment that allowed automakers to use advanced high-strength steels
- Integrating state-of-the-art prediction methods for assessing vehicle crash performance, which ultimately reduced physical testing requirements and enhanced product times to market
- Determining ideal local thermal processing procedures to tailor microstructures in critical sheet-metal components, which increased overall product safety and allowed a wider range of base materials
Other new innovations we’ve developed include conductive heat welding, resistance hole repair, and resistance pipe cladding.
Identify.
Develop.
Implement.
WE MANUFACTURE INNOVATION.
By developing novel technical approaches using established processes, we help manufacturers turn their design challenges into tangible successes. No matter your industry, we’re ready to explore resistance and solid-state options for your job. When can we get started?
Our Approach
When you work with EWI, we don’t just develop a welding solution and ship it. We stay in close communication from your first engagement through implementation. We believe that thoughtful process development with our client throughout a collaboration is key to a successful project.
“EWI’s understanding of the fundamental science of these technologies allows us to create highly customized solutions for special applications.”
— Jerry Gould, EWI Senior Technology Fellow
View Resistance Welding & Solid-state Processes Resources
Technical Expertise
EWI’s resistance welding and solid-state experience runs deep. The following are some of our most sought-after areas of expertise:
- Resistance welding, including spot and projection welding
- Capacitive discharge (CD) solid-state welding
- Low-force friction welding, aka translational assisted welding
- Rotary friction welding
- Linear friction welding
- Friction stir welding
- Resistance-based repair technology
- Metallurgical assessment
Equipment & Lab Resource
Resistance Spot Welding (dedicated) Systems
- ARP Electric Servo Gun
Resistance Spot/Projection Systems
- 30-kVA press welder
- 75-kVA press welder
- 100-kVA press welder
- 200-kVA press welder
Large Projection Welding Systems
- 600-kVA DC press welder
- 500-kVA frequency converter welder
- 600-kVA DC press welder (with vacuum chamber)
Resistance Seam Welding Systems
- 5kVA micro-seam welder
- 50-kVA large throat seam welder
- 200-kVA large throat seam welder
- 200-kVA direct drive seam welder
Capacitor Discharge Systems
- 5-kJ polarity switching CD system
- 20-kJ multi-capacitor bank CD system
Forge Welding Systems
- F3 low force friction welding upset system
- Low force friction welding system
- F6 flash/upset welding system
Pulse Welding Systems
- 20-kJ magnetic pulse welding system
- Electro-spark deposition system
Friction Stir Welding Systems
- GTC Accustir Friction Stir Weld
Friction Stir Spot Welders
- Harms and Wende Refill Friction Stir Spot Welder
- MILCO Low Cost FSSW Gun
Inertia Friction Welders
- MTI 120B
- Caterpillar 250A
- MTI 90B
Linear Friction Welder
- APCI/Taylor Windfield 15-ton Mechanical LFW
Additional Power Supply Arrangements
- MFDC inverters up to 2000A
- MFDC transformers up to 1600-kVA
Ready to take on your material joining challenges?
Contact EWI. We can help make things simpler.