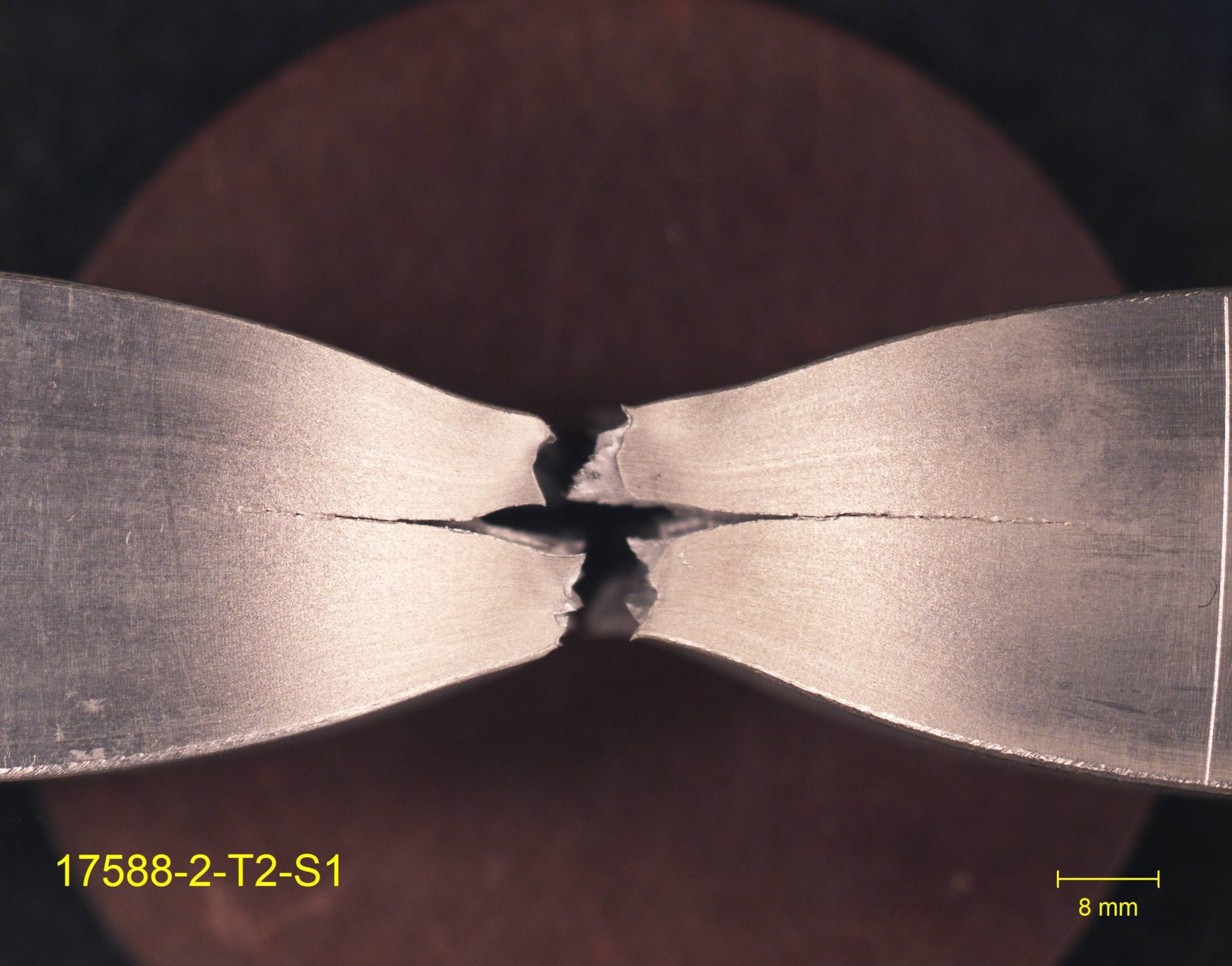
Structural Integrity
Structural integrity is the measure of a component’s ability to hold together without breaking or deforming.
Ensuring structural integrity is critically important for pipeline operators, automakers, oil and gas companies, ship builders, and manufacturers of industrial machinery.
Structural integrity not just a matter of strength testing and weld failure analysis – it’s about developing the most trustworthy methods for determining material properties, predicting damage in advance of application, and having the expertise to interpret and analyze results with accuracy and precision.
Since EWI’s founding, we have leveraged our extensive welding, materials, and finite-element-analysis capabilities to deliver comprehensive structural integrity assessments. These assessments – based on material testing, design analysis, fabrication methods and loading conditions – enable our clients to push the envelope in materials performance. Our structural integrity expertise includes:
- Material preproduction qualification testing for offshore oil and gas infrastructure
- General fracture toughness and fatigue analysis of welded joints
- CTOD, J, R-curve, fatigue crack growth rate, fatigue life characterization (S-N curves)
- Time-dependent fracture tests (step-wise incremental loading, sustained load cracking, etc.)
- Development of spot weld failure parameters for full-vehicle crash modeling
Direct Access to Structural Integrity Expertise
For more than 30 years, structural engineering professionals have turned to EWI to develop new ways to gauge fitness for service, and to devise new methods for preventing failure.
Our early efforts in weldability and advanced material evaluation set many standards for structural integrity, and our work in resonance fatigue, fracture toughness, corrosion modeling, and RP2Z testing have helped companies across industry assure structural soundness and safety in their products.
With recent innovations in areas such as modeling of low constraint fracture toughness test methods, improved joint design for lightweighting, and experimental fracture mechanics for pipelines, EWI continues to expand structural integrity options and solutions for fabricators across industry. EWI’s structural integrity specialists help our clients stay at the forefront of their industry.
Identify. Develop. Implement.
Why Choose EWI for
Structural Integrity?
EWI has been engineering with integrity since 1984. Whether our engineers are performing increasing loading tests on high-strength steel exposed to simulated seawater or assessing the wind-induced vibration resistance of utility tower weldments, we’re committed to the success of our clients.