
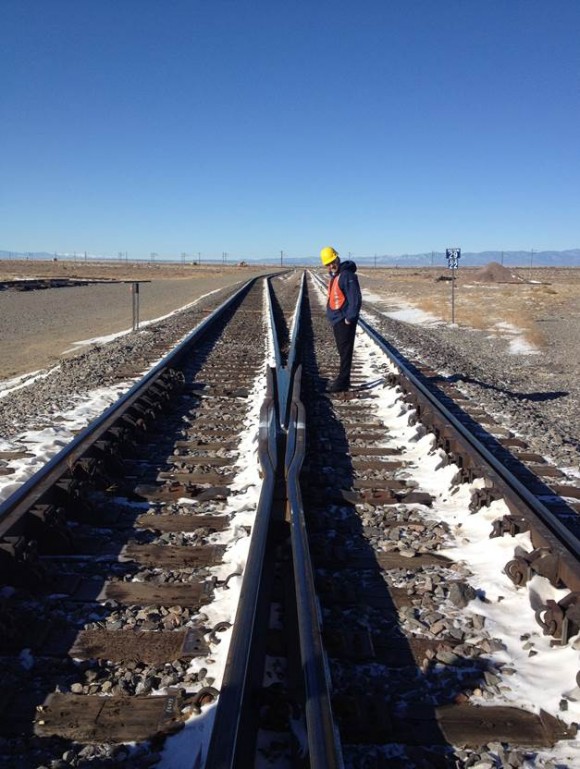
I recently rode my bicycle across America and saw a whole bunch of craziness: A hurricane in Maine, hail storms in the Arizona desert, a haboob in the California sand dunes, and hundreds of giant frogs…giant steel frogs…more specifically, giant battered austenitic manganese-steel frogs!
No, I didn’t lose my mind cycling for 43 days alone. I’m talking about a type of special trackwork used by railroads which allows track to converge, diverge, or cross. These components take a serious beating on a daily basis, and must be repaired due to wear, fatigue cracks, or when the train’s wheels simply rip a chunk of damaged material out as they make a transition (a.k.a. a “breakout”). It turns out that these battered frogs require the most maintenance of any track component and are unsurprisingly the most expensive to keep in good working order.
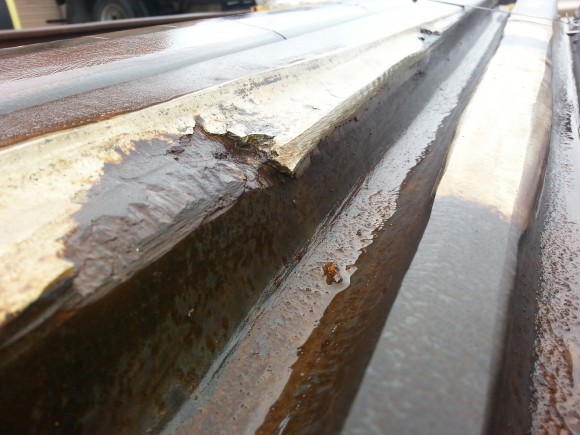
Here’s the kicker – While austenitic manganese steel (AMS) has some great qualities (high toughness and great work-hardenability), it’s a bit tricky to weld. Unlike typical rail steels, AMS does not respond well to high preheat and interpass temperatures. When this material gets too hot carbide precipitation occurs and it loses much of the toughness that makes it so attractive for this application. As such, the temperature of the base material must be kept unusually low. This impacts productivity negatively, making it difficult for repairs to be completed properly within the time allotted. In addition, since repairs are currently made with manually applied shielded metal arc welding (SMAW) and flux cored arc welding (FCAW), adherence to strict interpass temperature limitations is up to the individual welder and can’t be easily controlled.
EWI has conducted a project sponsored by the Federal Railroad Administration to develop a better method of repairing these components. Through a partnership with the Transportation Technology Center, Inc., and with guidance from the CSX corporation, EWI successfully used automated FCAW to achieve impressive results. Laboratory testing has revealed that EWI’s automated FCAW frog repair process results in a significant improvement in weld quality, reduced interpass temperatures, and increased productivity. The real proof is in the performance of these welds during in-track testing at Transportation Technology, Inc. (TTCI).
The life of rail components is measured in million gross tons, or MGTs. When an AMS frog is new, it will typically last between 55 and 60 MGTs before repair is required. Once a repair is performed this number drops to between 30 and 35 MGTs, provided that proper repair procedures are followed. A frog repaired with EWI’s automated FCAW process is currently being tested by TTCI and has accumulated over 90 MGTs to date. This is nearly triple the typical life of a repaired AMS frog and 50% more MGTs than a new frog, and testing hasn’t ended yet.
If you’re stomach turns at the thought of a battered frog, give Marc Purslow a call at 614.688.5150 or email him at [email protected].