
Springback is a critical challenge of forming and welding sheet metal and plate for manufacturing applications in aerospace, automotive, energy, electronics, and heavy manufacturing industries. Springback can complicate material properties, stress-strain variables, part geometry, frictions with forming tools, etc. It is difficult to eliminate springback during cold forming processes, but it can be controlled by compensating for the resulting dimensional change.
There are numerous considerations for welding formed parts where springback is present. For example, clamping forces in tooling must be adequately addressed to ensure optimum joint fit-up for welding. Reliable prediction and practical compensation of springback forces are imperative to maximized weld quality and stabilize fabrication processes.
EWI recently conducted research on springback in forming advanced high-strength steels (AHSS). In this study, the effect of elastic modulus on springback was investigated using various forming tests and finite-element method (FEM) simulation codes. The variations of elastic modulus for dual phase (DP) 600 and DP 780 sheet steels were characterized by conducting cyclic loading-unloading tensile tests. The non-linear mathematical form of elastic modulus was determined and implemented in FEM simulations to predict springback. To understand the effects of material properties on springback, relatively simple part geometries such as V- and U-shaped bending tests were studied first, with more complex shapes, such as the curved flanging and S-rail stamping, studied subsequently.
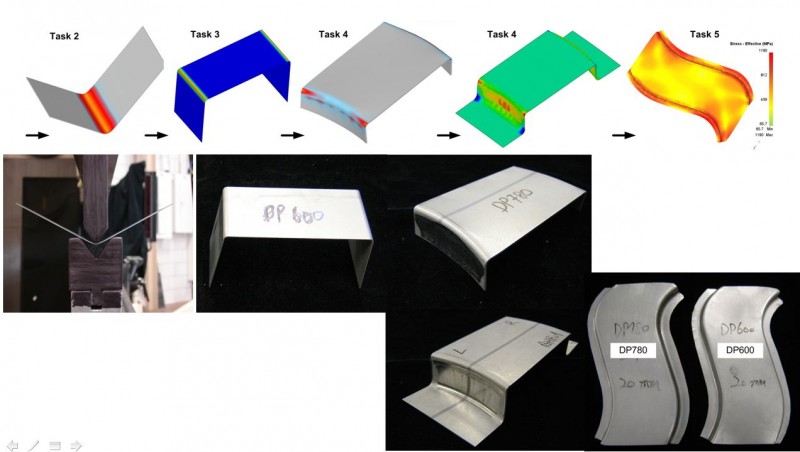
To obtain the accurate measurement data of springback, EWI utilized various advanced measurement methods, such as a high-resolution camera system with X-Y table and 3-D White Light Scanning, to measure the geometry of stamping parts. Two different commercial FEM codes, LS-DYNA and DEFORM-3D, were used in simulations of forming and springback for experiments. The shell-element model in LS-DYNA showed the better predictions of springback compared to the solid-element model in DEFORM-3D. The variable elastic modulus improved springback predictions with FEM in comparison with experiments.
For more information, please contact Dr. Hyunok Kim, Applications Engineer, Structural Integrity and Modeling. [email protected] 614.688.5239