
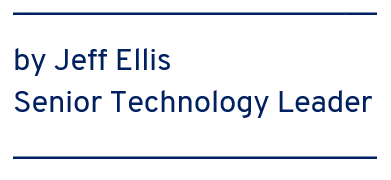
Polymers undergo creep and stress relaxation over long periods, which can be detrimental to the function of products in a multitude of industries. When designing devices or components that contain polymers, it is important to understand how to analyze stress relaxation vs. creep in plastic materials and develop mitigation strategies for the two phenomena.
Polymer Creep vs. Stress Relaxation
The major difference between creep and stress relaxation is the way stress and strain act upon them, as shown in this figure. For creep, a constant force is applied to the material and the material moves (ΔL). For stress relaxation, strain is imparted on the material, and the stress with which the material resists the strain decreases over time.
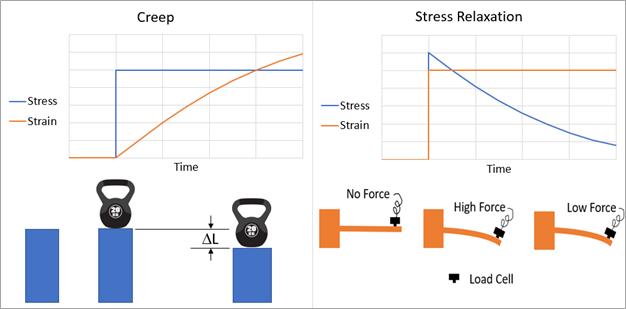
The following are real-world polymer creep and stress relaxation examples.
- Examples of creep in polymers:
- A large metal spring applies a nearly constant force on interacting parts as they slowly creep within a polymer auto-injector device.
- A plastic bandage is applied to a patient to hold an IV line in place. Over a couple of days, the constant stress on it causes the bandage to stretch and loosen.
- Examples of stress relaxation in polymers:
- A polymer spring is used to place a force on a vial to keep it aligned in a diagnostic instrument, but over time the force decreases and the vial becomes misaligned.
- An all-plastic clip is opened and fitted over a group of cables to manage their position. Over time, the clip applies less compression force and allows the cables to move.
What Causes These Material Property Changes?
The underlying reasons for creep and stress relaxation in polymers are the same and have positively correlated effects. For example, a polymer that has low creep will also have low stress relaxation. Both depend on how much relative motion occurs between polymer chains.
The motion – i.e., the cause of polymer property changes – is a function of one or more of these factors:
- Crystallinity of polymers – There are amorphous and crystalline polymers; some polymer chains pack into a crystalline orientation, and others do not. Crystalline regions pack much more tightly and neatly into organized structures than their amorphous counterparts. That compact structure greatly reduces polymer chain mobility. Since the crystalline polymer chains cannot move independently, polymers with a high crystalline percentage have low creep and stress relaxation. An example of a highly crystalline polymer with low creep is polyoxymethylene (POM).
- Polymer side groups – How do side groups affect polymer properties?Polymers with larger side groups have less relative mobility than those with small side groups and therefore have lower creep and stress relaxation. Envision a polymer chain as an extension cord. When you have many short extension cords, they easily slide over one another. Now envision that the extension cord has lights attached radially in every direction along its length. It is difficult to slide these light strands over one another. This demonstrates the difference between polyethylene (PE), which is like the extension cord, and polypropylene (PP), which is like the light strand due to larger side groups. The PP has lower creep and stress relaxation than the PE.
- Molecular weight (MW) – A confounding factor is the effect of molecular weight on polymer properties: The higher the MW, the longer the polymer chain, the lower the melt flow index, and the harder it is to get the polymer chains to move independently. Therefore, higher MW also has better resistance to (i.e., lower) creep and stress relaxation.
- Fillers and glass transition temperature – The effect offillers in polymers is usually a decrease in polymer chain mobility and an increase in the materials’ modulus; both cause lower creep and stress relaxation due to better resistance. For example, glass fibers are often used to reinforce nylon. There is a chemical compatibilizer called “sizing” that chemically links the glass to the nylon so that the polymer chains have difficulty moving relative to the glass, and vice versa. The glass has a much higher modulus than the nylon, so a glass-filled composite has a higher modulus than the neat polymer. When stress is applied to the filled nylon, less strain is imparted due to the higher modulus, meaning that the creep will also be reduced.
What Are Creep-Resistant Plastics?
We’ve just acknowledged the many materials science factors that affect creep in plastics. Temperature, stress or strain, and environmental conditions also play a role. Therefore, providing a foolproof list of creep-resistant plastics is not possible without knowing the full context of the intended product and application.
However, these are a few polymer materials that resist creep in many applications:
- Polyoxymethylene (POM)
- Polypropylene (PP)
- Polyethylene terephthalate (PET)
- Polytetrafluoroethylene (PTFE)
- Nylon
- Ethylene-chlorotrifluoroethylene (ECTFE)
Stress Relaxation and Creep Testing of Polymers
Long-term creep and stress relaxation can be estimated with short-term testing, which is useful for product development efficiency because creep and stress relaxation can take months or years to appear in normal use. EWI’s polymer research team implements time-temperature superposition (TTS) techniques using a dynamic mechanical analyzer (DMA) of polymers. The DMA can exert controlled stress or stain on the polymer at a specified temperature, as well as several elevated temperatures, throughout a series of tests. The elevated temperatures must not come within 10°C of the glass transition temperature because there is a step change in the polymer’s response that affects the accuracy of predicting future polymer performance at a lower temperature.
Once all the data has been collected, the higher temperature data points are superpositioned out to longer times, with the highest temperature being shifted to the longest time. Once shifted, all the data makes one master curve that predicts the long-term creep or stress relaxation. Time-temperature superposition testing can be completed in about one week and can predict a polymer’s response several years into the future.
Why Is This Testing Important?
When you want your products to last many years, even with constant forces pushing on them, it’s essential to consider long-term polymer properties during design and material selection. These steps are even more important if the products will be assembled years in advance of being used, as is the case for single-use medical devices like auto-injectors. The levels of stress or strain exerted on a material can be difficult to measure, but they can be modeled using finite element analysis (FEA) of polymers.
Ensure Product Longevity with EWI
Are you looking for engineering and materials science support? EWI supports any stage of product design or production for innovators in a variety of industries. We have strong knowledge of polymer properties and plastics joining, along with well-equipped research labs. From design consultation to thermal analysis to custom tooling, we’ll do everything we can to ensure your design and process are set up for optimal manufacturability before costs are sunk. Contact Jeff Ellis at [email protected] or (614) 688-5114 to learn more, or complete our contact form to connect with our team.
Read more about avoiding material failure in plastic products: