
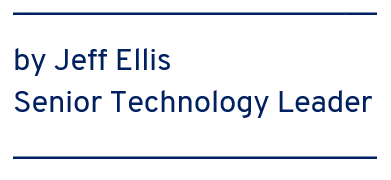
Polymers are more alive than you may realize. There are molecules within them that wiggle, others that move from here to there, and some that permeate all the way through. Polymer properties change as all this motion is occurring. When this is not understood or anticipated during product development stages, products fail.
The good news is that if we consider the product’s environment, we can choose a material that will ensure its longevity.
The Challenges of Polymer Permeability
The gas permeability of polymers can make or break the performance of materials in many applications, such as plastic packaging. Small gas molecules such as hydrogen, oxygen, and even water vapor constantly diffuse through polymers. They are small enough to fit between the amorphous polymer backbone chains and can cause issues for real-life products.
Likewise, there are polymer additives, such as plasticizers, that are mobile and move through the material. Plasticizers diffuse out of the polymer and leave the material less elastic and more brittle. Other additives, such as flame retardants or stabilizers, can also have adverse effects on products in certain environments; associated material failures can be thermal, chemical, structural, etc.
Here are six examples of product failures due to the barrier properties of plastics:
- That new car smell is from plasticizers leaving your dashboard and making it more vulnerable to cracking over time. The automotive industry’s engineering solutions must balance durability with the cost, manufacturability, and expected lifespan of the product.
- Oxygen permeates through packaging and reduces the shelf life of the food inside by rapidly spoiling it. Oxygen can also leak through seals in packaging; an EWI affiliate, UltraThinSeal™, found that ultrasonic seals for potato chip bags allow less oxygen permeation through polymers than heat seals do. See Figure 1.
- Hydrogen absorbs into elastomer seals for pumps and storage containers, which can cause catastrophic failure during decompression due to supersaturation and foaming.
- Water vapor (humidity) permeates into packaging. This causes caking of dry powder products like sugar, and it changes the composition of fluids like brake fluid.
- Water vapor permeates out of packaging, leaving liquid products with decreased volume and/or increased concentration. This can be an extreme issue in applications like liquid medicines.
- Water vapor absorbs into a plastic that is ultrasonically welded, leading to voids and low strength.
What Makes or Breaks a Polymer’s Longevity?
So, barrier properties are important for everyday applications—but how do these product failures happen? The type of polymer chain groups, crystallinity, solubility, and other factors are at play.
Gas barrier properties of polymers are affected by pressure or concentration gradients. Polymers attract like gas molecules, so a polar group on a polymer chain will absorb more water than a non-polar group. For example, nylon has polar side groups and it absorbs a relatively high percentage of water humidity from the atmosphere, while high-density polyethylene (HDPE) is non-polar and allows very little (0.01%). Therefore, HDPE has a lower water vapor transmission rate. Polymer barrier properties can be tuned to meet the needs for the product.
Crystallinity and fillers in the polymer affect gas molecule permeability. Spherulites are crystalline arrangements of polymer backbone molecules that pack much tighter than the amorphous regions. The tight packing excludes gas molecules from entering. Similarly, fillers such as glass and calcium carbonate also block molecules. To permeate through, the gas molecules must find a circuitous path around the obstacles in the polymer. So, polymers with high crystallinity or filler content typically absorb less gas and have lower permeation rates.
Additionally, solubility plays a role. The higher the gas solubility in the polymer, the more it increases the void space and thus allows greater polymer chain movement. This can relieve molded-in stress and, in extreme cases, deform parts. Higher absorption also allows for molecules, such as plasticizers, to diffuse within the polymer. These plasticizers can diffuse all the way to the polymer surface and render it stiffer and more brittle.
Measuring Permeation Rates in Polymers
Yes, the determination of oxygen and water vapor permeability of polymers is possible. Permeation rates of other gases through polymers can be measured as well.
One of the most popular and accurate instruments for barrier-testing polymers is a permeation analyzer. During testing, a film of the material is clamped into the instrument. One side is exposed to the gas of interest (e.g., oxygen or water), and the other side is flushed with an inert gas (e.g., nitrogen or argon). There is a detector on the flushed side to determine when the gas of interest permeates through the material.
Solubility, diffusivity, and permeability can all be determined from this measurement. The permeation rate is typically linearly dependent on the gas concentration and exponentially dependent on temperature.
No matter the method, it’s critical to consider and test the barrier properties of polymers when choosing a material for a product. Additionally, test in the right context—the product’s intended environment and expected lifespan both affect predictions and modeling of how much gas will absorb and permeate through the polymer. This can give you a clear picture of the risk of product failures that would affect consumers.
Are you experiencing barrier diffusion issues with your plastic products? EWI’s polymer materials engineers can help. With an experienced team and well-equipped research labs, we support any stage of the product design cycle and are up for any challenge. Contact Jeff Ellis at [email protected] or (614) 688-5114, or contact us online to connect with our team.
Read more articles about avoiding material failure in plastic products: