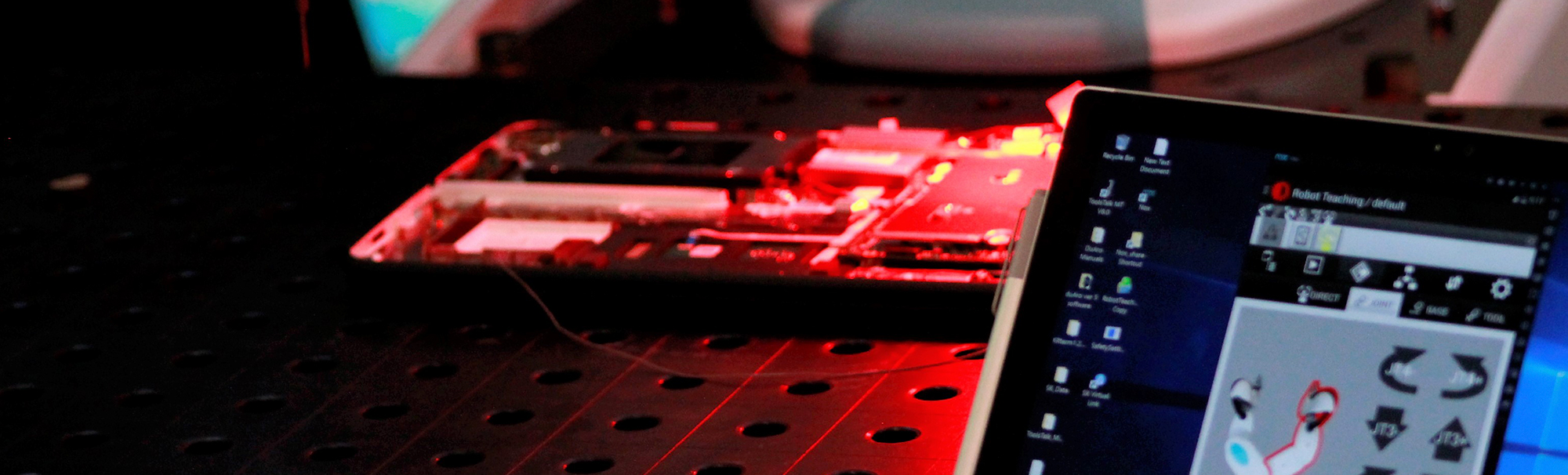
Advanced Automation
How, where, and when do you integrate automation into your manufacturing process?
Smart technology paired with technical skill and expertise can produce game-changing results.
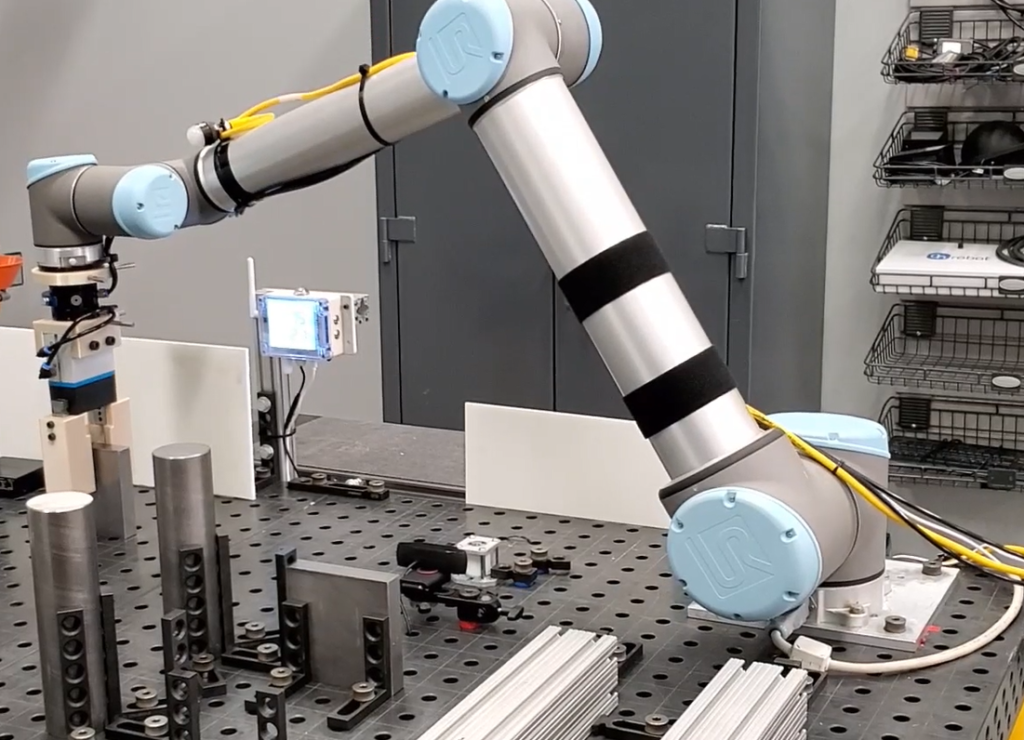
Automated processes and robotics have long been used to handle the physically difficult, repetitive, and even dangerous tasks previously performed by humans. They have also helped address lack of skilled labor in several industries.
Today’s advanced automation, however, is not about replacing people. On the contrary, it combines the best of automated technology – visual inspection, machine learning, and artificial intelligence, for example – with the experience and skills of technically trained experts to produce the highest-quality products at top productivity levels.
EWI helps organizations identify, develop, implement, and train staff on new automation technologies. Our team works with organizations of all size, from small local manufacturers to large multi-national organizations. We go beyond robotic hardware to support and complement automation technologies that can help you increase productivity, upskill your teams, and mitigate the impacts of workforce shortages.
EWI focus areas include:
- Advisory Services – Providing expert guidance to identify high-impact automation opportunities for current and planned manufacturing operations
- Training – Training on collaborative and industrial automation systems through structured classes and application/system specific training.
- Collaborative Robots (Cobots) – Novel implementations of cobot and mobile automation technologies to address immediate manufacturing needs and ongoing workforce challenges.
- Tele–manufacturing – Pioneering new technologies that enable real-time remote control and sensory feedback from robotic systems in manufacturing, fabrication, and service industry environments.
Direct Access to Automation Experts
From developing a robotic vision-guided sealant application process to developing a test bed for laser powder bed fusion additive manufacturing, our team greets new automation challenges with enthusiasm. We’re creative problem solvers with a passion for finding out-of-the-box solutions for your most complex automation challenges. And we’re excited to learn more about your automation project.
Identify. Develop. Implement.
Why Choose EWI for Advanced Automation?
Our team has helped companies small, mid-sized, and large with manufacturing automation. We are prepared to assist you with collaborative and industrial robot programming, advanced sensor and machine vision expertise, haptic feedback and advanced control development, robotic system integration, and automation training.
Check Out EWI’s
Automation Training Classes!
Advanced Automation Resources
You can access EWI papers, videos, presentations, and case studies related to advanced automation by clicking below:
Technical Expertise
- Flexible and fixed automation solutions for welding and inspection
- Collaborative, human–robotic processes
- Pick-and-place, palletizing, bin-picking, part-feeding, and delivery systems
- Fixture and tooling design for automated systems
- Discrete event simulation and robotic cell simulation
- 2D and 3D machine vision systems
- EWI-developed force-control sensing
- Automated nondestructive evaluation (NDE), real-time process monitoring, and machine tending
Equipment & Lab Resources
A wide variety of equipment is available across EWI’s locations to support your automation project. This includes:
- A large array of cobots from Universal Robots, Doosan, and other manufacturers
- Industrial robots from Fanuc, ABB, Yaskawa, and other leading robotics companies
- Advanced vision and inspection technology, including 2D and 3D vision, 2D laser profilers, and more
- A wide assortment of end-of-arm-tooling (EOAT) including grippers, welding systems, automated screwdriving components, and more
- Safety systems including lights screens and area scanners
- Various supporting components such as sensors, conveyors, motion components, actuators, pneumatics, and controls
- Production-grade 3D-printing systems for both rigid and flexible materials