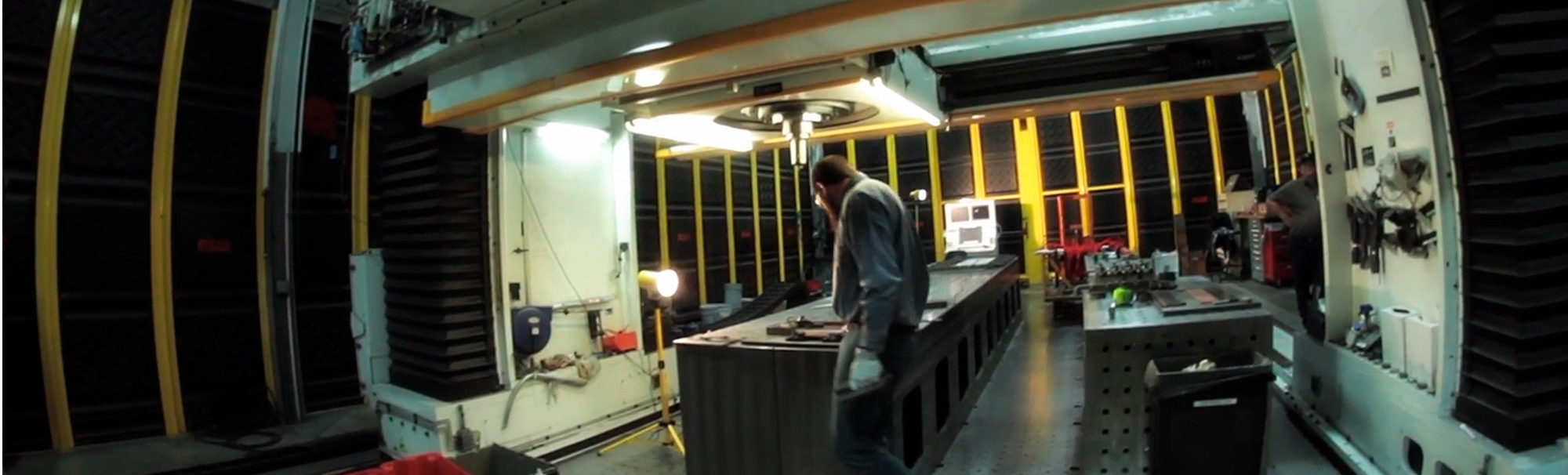
Welding & Joining
EWI was founded to advance welding and joining technology.
Welding held us together in our early years and was the foundation of our growth into the engineering innovators we are today.
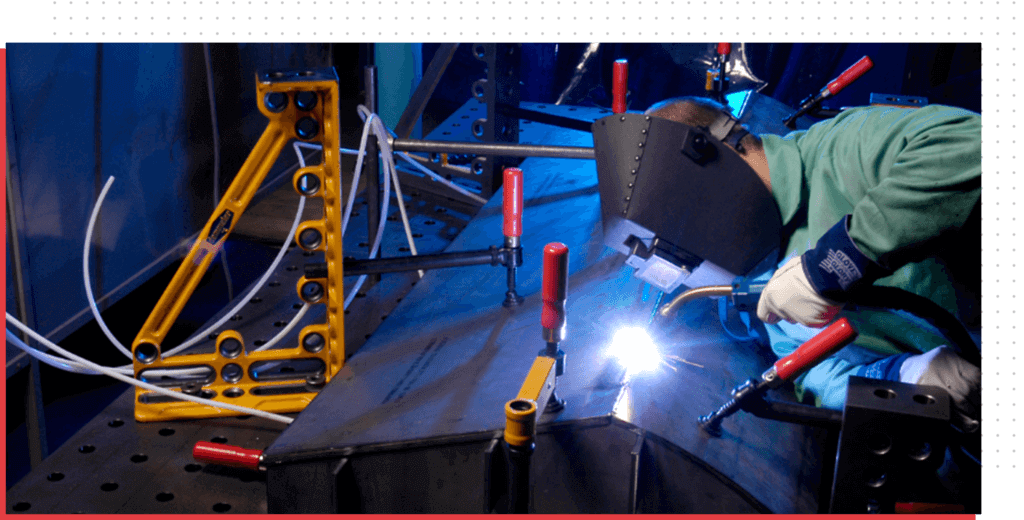
Over time, we’ve stayed true to our welding roots while redefining the limits of industrial joining processes, developing game-changing techniques for both fusion and solid-state processes. Welding and joining remain core services at EWI, but we have a much more advanced suite of capabilities than we did in 1984.
Our Welding & Joining Capabilities
In our work, we use state-of-the-art equipment and in-depth experience to develop accessible solutions for emerging applications. Let us help you leverage the following welding technologies:
To view demonstration videos of our welding and joining capabilities, click below:
Identify. Develop. Implement.
Why Choose EWI for Welding & Joining Services?
Over the last three decades, EWI has developed many specialized welding solutions for unique applications in different industrial sectors. Our welding and joining engineers are not afraid of a challenge. If your project is sensitive or exceptional, you can trust our welding and joining experts to meet your needs, from conceptualization to the production line.
Check Out EWI’s Welding Engineering Courses!
Course Offerings
EWI offers several useful products to enable and improve in welding processes.
View Welding Products