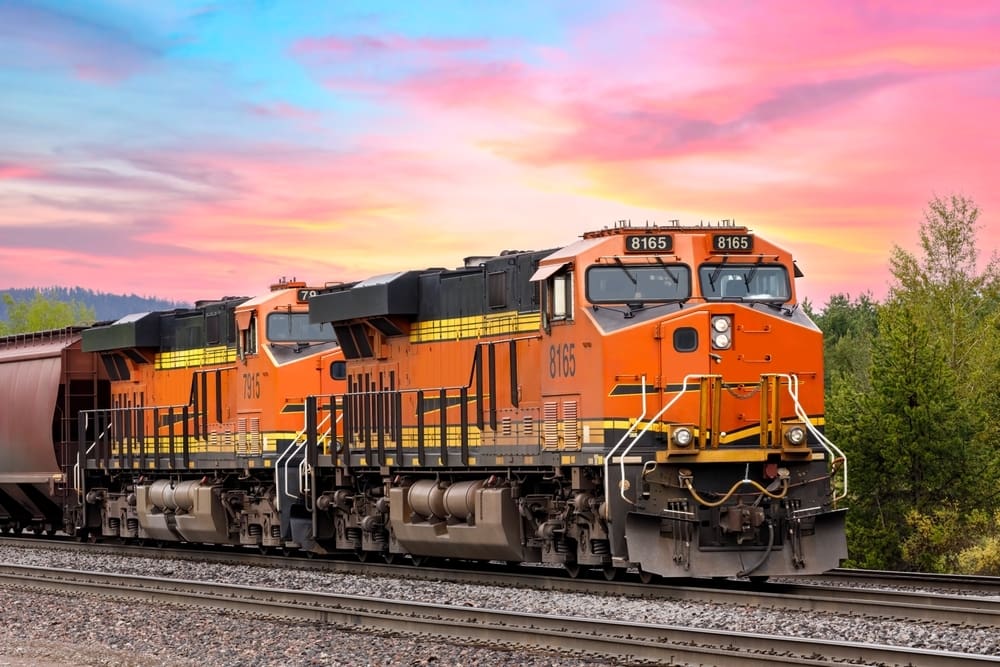
Industrial Equipment & Heavy Manufacturing
Despite skilled labor shortages in manufacturing, heavy industry is pursuing new opportunities through advanced automation and new material technologies.
EWI offers engineering services to help you optimize your operation and improve your productivity. We have deep expertise in heavy manufacturing process automation, joining process development, materials evaluation, NDE, and advanced data analytics.
Your Heavy Industrial Manufacturing Consultants
Agility in heavy industry manufacturing can be a huge challenge. Traditional processes are slow and hard to alter, automation is expensive, the workforce is shrinking, and new materials – though attractive – present many unknowns. How can a company continue to improve its processes and stay competitive?
EWI’s advanced manufacturing teams can help, whether you want to improve product durability, minimize fatigue, weld thick plates faster, integrate automated solutions, or introduce flexible manufacturing processes. EWI is ready to apply our industrial equipment and heavy manufacturing engineering expertise and onsite resources today to ensure your company’s success.
Key services include:
- Tele-manufacturing
- Structural modeling and ICME
- Nondestructive evaluation and inspection
- Quality assurance
- Advanced materials science
- Arc welding and DED
- Laser welding
- Automation
- Data science
Industry Sectors
- Shipbuilding
- Construction
- Mining equipment
- Agricultural equipment
- Rail
Learn more about our solutions for these sectors.
EWI can help you identify your challenges and opportunities, develop ideal processes, and implement your technological innovations.
Want to learn more?
Check out EWI’s research, video demonstrations, and service overviews for the industrial equipment and heavy manufacturing sector.