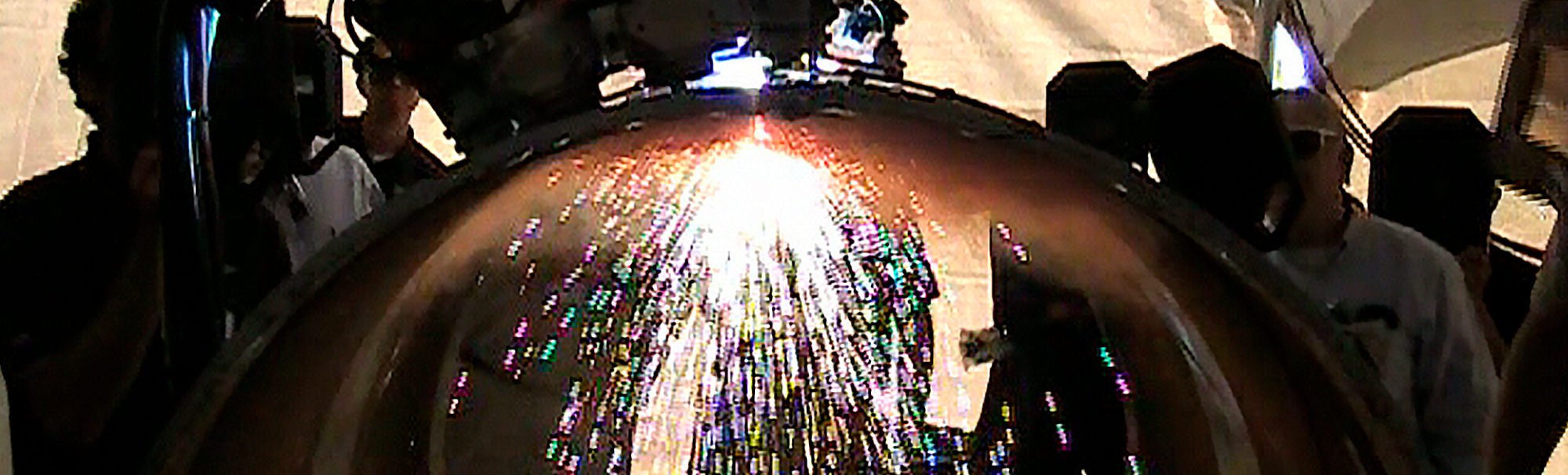
Arc Welding & Directed Energy Deposition
Our Arc Welding Expertise
Since EWI’s founding in 1984, we have been enhancing and optimizing arc welding processes to the benefit of all manufacturing sectors.
Specializing in welding, cladding, repair, large-scale additive manufacturing, and more, EWI has developed and launched technologies for applications ranging from ship building and jet engines to oil and gas fabrication.
Because so many of our clients have unique goals, we focus on not only the deliberate application of arc welding technology but also on lesser-considered – but highly important – systemic details:
- Leading cross-process projects – e.g., combining arc welding with nondestructive evaluation (NDE), simulation and automation
- Creating remanufacturing applications
- Developing novel repair technologies for highly engineered alloys
- Guiding the implementation process through completion
EWI is an industry leader in consumable and non-consumable electrode arc welding processes. Our expertise is broad, and we keep it that way with relentless innovation. We’ve developed specialties in progressive arc-based applications for complex metal builds and repairs, One such specialty is arc directed energy deposition (DED).
DED is a cutting-edge type of additive manufacturing using a robotic arm, an arc, electron-beam or laser-beam process, and either powder or wire for complex metal builds. For many applications, DED can be faster than other methods of additive manufacturing, and its accuracy reduces the need for machining after an additive part has been produced. At EWI, we can utilize CAD-to-path (robotic path planning) to build at multiple angles. This allows us to not only build solutions for new applications but also to use DED for making repairs and adjusting features.
Our Approach
In order to efficiently leverage the arc-based processes we know so well, we approach each project with careful attention to developing procedures and complying with applicable standards and codes. These are important aspects of our arc welding engagements – just as important as the technologies themselves.
- Parameter development and optimization
- Procedure development
- Adherence to codes and standards
- Design for welding and design reviews
- Customized training
- Process comparison and down-selection
- Feasibility studies
- Feature-based qualification
- Cooperative research programs
- Site evaluations
We greet tough goals with excitement, leveraging cross-departmental strengths and staying engaged with our clients from idea to production. With this perspective, we’ve developed arc welding solutions for these unique applications:
- Formulating EWI DeepTIGTM compounds to provide consistent GTAW joint penetration
- Applying reciprocating-wire-feed GMAW to components made of crack-sensitive material – surrounding heat-sensitive fluid and components – without the use of preheat
- Automating the repair of austenitic manganese steel trackwork components for the Federal Railroad Administration, increasing the service life of these expensive high-wear components by over 200% and reducing lost track time
- Investigating the effects of welding techniques, electrode chemistry, and shielding gas on GMAW stainless steel-clad layers for a fabricator of nuclear components and vessels
Identify. Develop. Implement.
Authoritative & Innovative
Through inventiveness, our clients’ trust and collaboration, and decades of combined experience, our arc welding team has accomplished considerable feats – from setting industry standards for GMAW procedures to enabling intricate welds strong enough for outer space. Let EWI meet your organization’s challenges.
View Arc Welding & Directed Energy Deposition Resources
Getting the Most Out of Tandem GMAW: For the Fearful and the Frustrated
Tandem gas metal arc welding (GMAW) is not a new technology. Although it boasts a number of enticing benefits over [...]
Technical Expertise
Core arc welding competencies:
- Directed energy deposition (DED) Additive Manufacturing (AM)
- Large-scale DED AM
- Adaptive welding
- Precision & orbital GTAW
- RP2Z base material qualification welding techniques
- Temper-bead welding
- Cladding and hardfacing
- Narrow-groove welding techniques
- Pulse waveform development
- Out-of-position GMAW / GTAW
- High-speed welding techniques
Cross-cutting tech competencies:
- Process and procedure optimization
- Distortion control technologies
- Onsite troubleshooting
- Assembly tooling
- Automation and mechanization
- High-speed data acquisition and video
Equipment & Lab Resources
Power supplies ranging from 0.02 to 2000 A from suppliers:
- Cloos
- ESAB
- Fronius
- Liburdi
- Lincoln Electric
- Miller Electric
- OTC-Daihen
- Panasonic
- Secheron
DED AM technology & Systems:
- Basic Autodesk PowermillTM Training Services
- IR-based Preheat & Interpass Control
- Thermal Management Technology
- High Duty Torch Apparatus
- Binzel
- Cloos
- Sciaky EBAM 110
- RPM 557
- Arc DED Robot Systems:
- 7-axis Motoman Fronius CMT GMA-P DED
- 8-axis OTC GMA-P / Hot Wire GTA DED
- 8-axis OTC SyncroFeed GMA-P DED
- 9-axis Cloos Dual Tandem GMA-P & Motion GMA-P DED
- 14-axis Genesis Dual 6-axis Fanuc GMA-P DED
- 11-axis Navus ABB Multi-Process Gantry (July 2020)
Orbital welding systems:
- Arc Machines Inc.
- Swagelok
Mechanized side beams and tracks with carriages:
- Bug-O
- Gullco
- Jetline
- Lincoln Electric
- Pandjiris
Interested in our Arc Welding & Directed Energy Deposition expertise?
Contact us to learn what we can do for you.