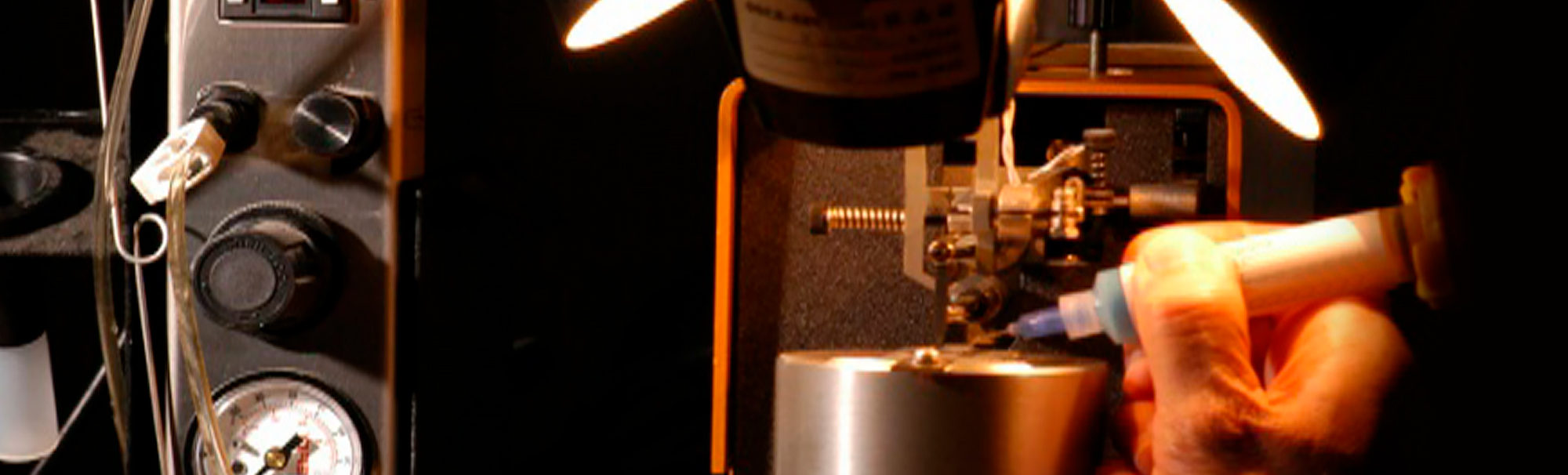
Plastic Welding
Engineering polymer joining for robust products.
When you’re working with polymers during any stage of product development or production, it’s a challenge to ensure strong, well-sealed welds without compromising component design. EWI can help you develop custom plastic welding solutions.
From plastic welding consulting to process modeling to evaluation, we do more than just find ways to join polymers and dissimilar materials. Our engineers can help you identify which plastic welding process to use (or create a new one), optimize product design for manufacturability, validate the process, guide your team through implementation, and support training and production launch.
Ideally, we start working with our clients at the beginning: part design and process development. Manufacturers that bring us in at a later stage often need to analyze a failure, develop an approach for plastic welding repairs, or redesign tooling or processes.
Our more unique plastic welding R&D capabilities include:
- Custom-designed tooling and process validation, including for ultrasonic welding of plastic and laser welding of plastic
- Plastic weld quality evaluation, including CT scans and diffusion analysis
- Deflection, vibrational mode, and heat generation modeling of plastic joining processes
- Plastic welding consulting – material selection, design evaluation, joint recommendations, and material weldability studies
Our Experience with Polymer Welding Technologies
EWI has a 30-year history of engineering plastic welds for innovations in all manufacturing sectors. Our industrial expertise and excellent lab facilities position us to support diverse applications, from micro-welded plastic medical devices and electronics to big-and-strong (yet light) parts for aerospace.
We go all in to meet our clients’ goals, and we’ve been instrumental in breakthroughs over the years, including:
- Developing a method to structurally bond a polymer to metal without adhesives.
- Conducting R&D on the effect of joint design on ultrasonic welding of polybutylene terephthalate (PBT), which proved that a less-expensive, longer-lasting energy director could be used with servo motion control during ultrasonic plastic welding.
- Receiving a patent for ultrasonic technology UltraThinSeal™ for high-speed package film sealing that can be easily integrated into most standard thermal sealing bagmakers.
Identify.
Develop.
Implement.
WE MANUFACTURE INNOVATION.
Whether we’re working with automotive OEMs, consumer electronics companies, solar power companies, or aviation giants, we bring big ideas to fruition. With EWI, you can always expect intelligent, creative solutions based on our extensive expertise in plastic welding techniques.
Support When You Need It
Whether you engage EWI services at the beginning of your project or mid-process, we’ll make your challenges our mission. We promise to keep you informed about materials feasibility and guide you toward a high-quality, cost-effective, environmentally viable process. Fill out the form below to get the support you need.
View Plastic Welding Resources
The Crazy Brilliance of Radio Frequency Welding
When it comes to welding plastics, three contributing factors matter: heat, force, and duration. While there are multiple ways of [...]
Technical Expertise
These are the core processes of our plastic welding services and related services:
- Ultrasonic welding and related processes (swaging, cutting, sewing, and more)
- Laser welding and surface treatment
- Infrared welding (through-transmission and standard)
- Spin welding
- Vibration welding
- Friction stir welding
- Thermal welding (staking, hot plate, hot tool, film sealing, etc.)
- Extrusion welding
- Hot gas welding
- Implant and radio frequency induction welding
- Resistive implant welding
- Adhesive bonding
Testing & Analysis
No process is complete without thorough testing and analysis. Here is a selection of techniques we employ to be sure we’re developing the most effective plastics solution:
- Dynamic mechanical analysis (DMA)
- Differential scanning calorimetry (DSC)
- Rheology
- Thermogravimetric analysis (TGA)
- CT scanning
- CT metrology for dimensional analysis
- Material selection and weldability testing
- Joint and tooling design
- Fourier transform infrared (FTIR) spectroscopy
- Microscopic analysis
- Air decay leak testing
- Diffusion analysis – Heated After Cross Section (HACS)
- Mechanical testing (tensile, shear, peel, push, impact, etc.)
- Accelerated aging
- Degradation modeling
- Failure analysis
Equipment & Lab Resources
- Hot Plate/Infrared (IR)
- Custom system with dual-temperature capability enabled
- Ultrasonic welders:
- 40 kHz Branson, servo
- 35 kHz MS Ultrasonic, servo
- 30 kHz Dukane, servo
- 20 kHz MS Ultrasonic, servo
- 20 kHz Dukane, servo
- 20 kHz Dukane, pneumatic
- 20 kHz Branson, pneumatic
- 15 kHz Dukane, servo
- Laser welders:
- Extol Workcell with 2-micron wavelength laser
- Variety of 1-micron wavelength laser systems
- Induction generators:
- Ambrell HotShot 7.5 kW power supply, 150-400k Hz
- Seit 1TM, 2.8 kW, 700-1100 kHz
- Spin Welder:
- 3000 rpm Dukane, dual servo
- Resistance:
- Amada-Miyachi Uniflow 4, 2 kVA power, up to 600C
Polymer to polymer, polymer to non-polymer, never-been-tried-before materials?
Let us know the goal.